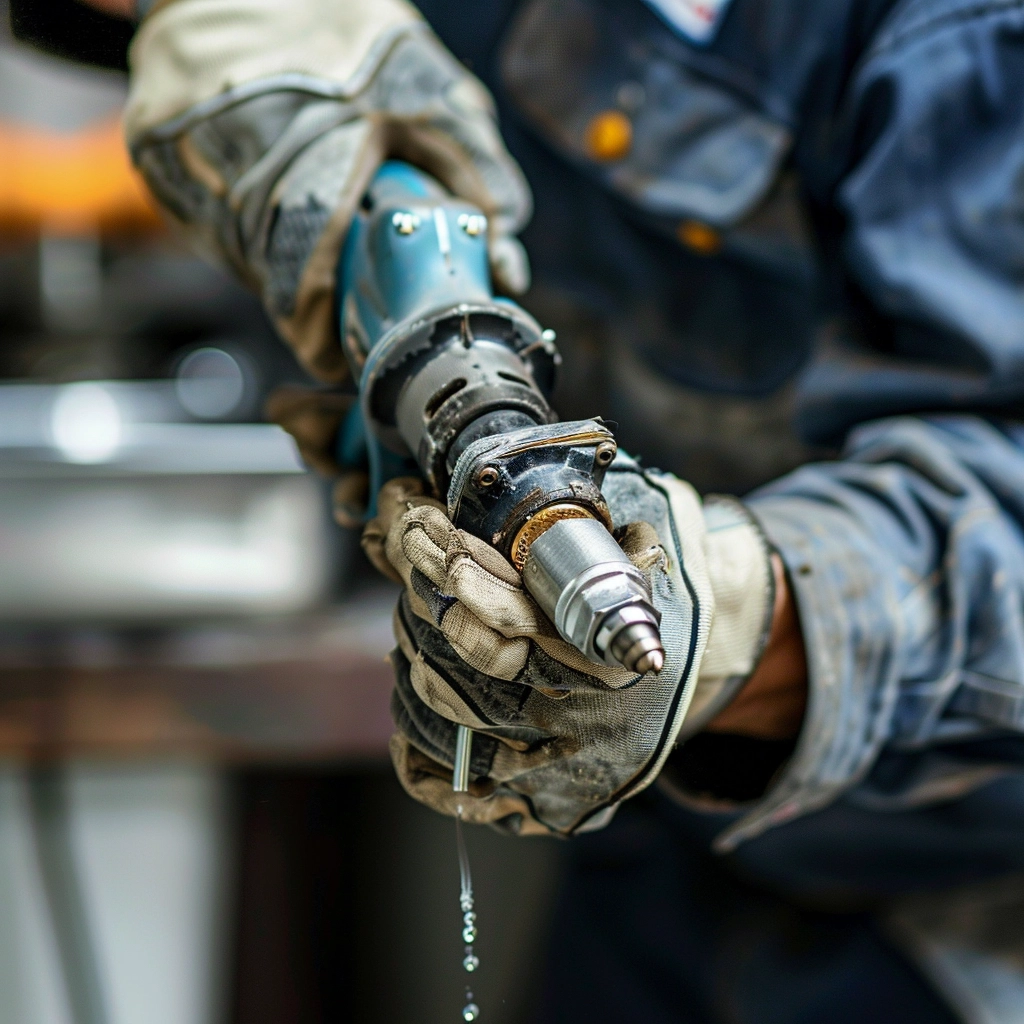
Dive into the essential strategies to enhance the performance and extend the life of pneumatic tool, vital in industries such as construction, automotive, and manufacturing. This guide offers practical advice for the upkeep of pneumatic power tools including pneumatic impact wrenches, screwdrivers, airbrushes, angle grinders, air hammers, and pneumatic drills, ensuring they operate at peak efficiency and productivity. Regular inspection and maintenance, including for air motors, air sanders, and pneumatic torque wrenches, are key to maintaining optimal tool performance. Incorporating pneumatic tool maintenance, along with care for pneumatic grinders, die grinders, pneumatic chisel, pneumatic screwdrivers, pneumatic cutting tools, and pneumatic riveting tools, ensures comprehensive care.
Maintaining Air Quality for Pneumatic Tools
Start by ensuring a clean, dry air supply to your pneumatic tools to ward off internal corrosion and performance degradation. Investing in top-notch air filters and regulators is essential to maintain the highest air quality, thereby enhancing the durability of air compressors and compressed air systems, fundamental for efficient dust extraction in a dry environment. Including
Adjusting Air Pressure for Tool Efficiency
Pneumatic tools thrive within precise operating pressure ranges. Employing dependable pressure regulators to manage air power is crucial, ensuring your tools work within the ideal pressure range for top performance and energy efficiency, a practice known as effective pressure management. This is a cornerstone of a well-optimized pneumatic setup.
Routine Maintenance Schedule for Pneumatic Tools
Establishing a regular maintenance schedule is crucial for extending the lifespan of your pneumatic tools. This regimen should include lubricating moving parts, checking for wear and tear, and replacing worn components in a timely manner, all of which are vital for maintaining tool performance and safety. Such diligent pneumatic tool maintenance is key to ensuring longevity.
Regular Maintenance: Prolonging Tool Lifespan
Adhering to a routine maintenance schedule is paramount for your pneumatic tools. This involves lubricating moving parts, performing inspections for wear and tear, and swiftly replacing worn-out components. Consistent tool maintenance and routine cleaning not only ensure optimal performance but also extend the life of your tools, highlighting the importance of tool safety and inspection. This practice embodies the essence of pneumatic tool maintenance.
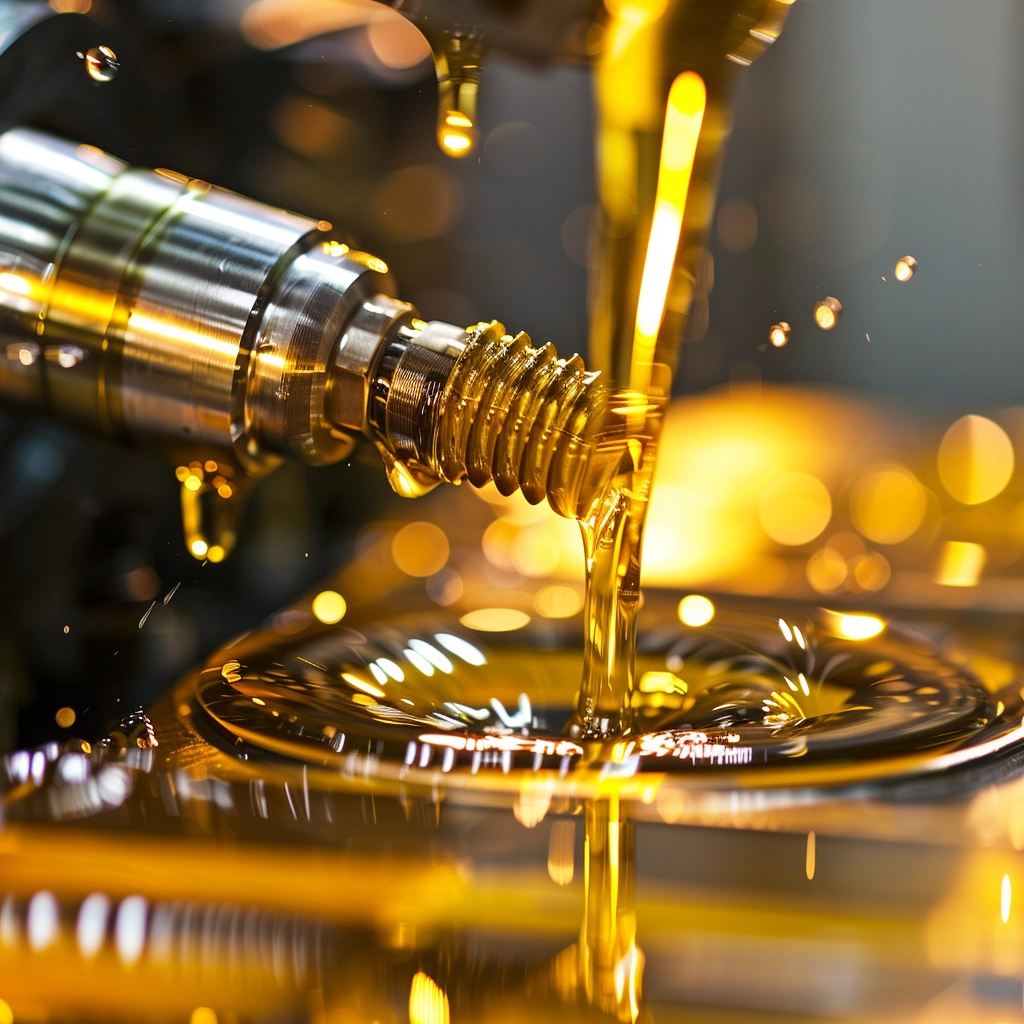
Choosing the Best Lubricants for Air Tools
Lubrication is key to the smooth operation and longevity of pneumatic tools. Opt for high-quality pneumatic tool oil recommended by the tool’s manufacturer and apply consistently to the tool’s air inlet to preserve optimal internal functionality, a practice known as air tool lubrication. This is an integral part of pneumatic tool maintenance.
Managing Duty Cycles in Pneumatic Tools
Understanding and managing the duty cycles of your pneumatic tools is critical to avoid overheating and premature wear. Make sure your tools are given adequate cooldown periods during extensive use to maintain peak performance and safety, while also being mindful of preventing accidental activation.
Ensuring Air Tightness with Quality Pneumatic Fittings
Air leaks can drastically reduce pneumatic system performance. Employ high-quality fittings and connectors to minimize air leakage, conduct regular checks for leaks, and replace defective parts to ensure efficient compressed air usage and system integrity. Regular inspection of air hoses can also help in identifying and rectifying any leaks early on. This vigilant approach is a key aspect of pneumatic tool maintenance.
Selecting the Right Tools for Specific Jobs
Selecting the appropriate tool for each job is essential for maximizing performance and preventing unnecessary wear. Ensure the pneumatic tool, especially screwdrivers, is suitable for the task at hand
- Performance Efficiency: The right tool ensures that tasks are completed efficiently and effectively.
- Tool Longevity: Using a tool suitable for specific tasks prevents premature wear and tear.
- Operational Costs: Proper tool selection can reduce costs by minimizing downtime and maintenance needs.
- Safety: Appropriate tools reduce the risk of accidents, as they are designed for specific tasks and conditions.
- Work Quality: Correct tools achieve higher quality results, ensuring precision and effectiveness.
This comprehensive approach not only improves the efficiency and productivity of pneumatic tools but also significantly boosts the overall safety and quality of work across various industries.
Conclusion
Enhancing the performance of air tools requires diligent maintenance, regular inspections, and a commitment to using the right tools for specific tasks. By adhering to these comprehensive maintenance top 5 safety guidelines when using pneumatic tools, which further support the reasons to enhance pneumatic tool performance.