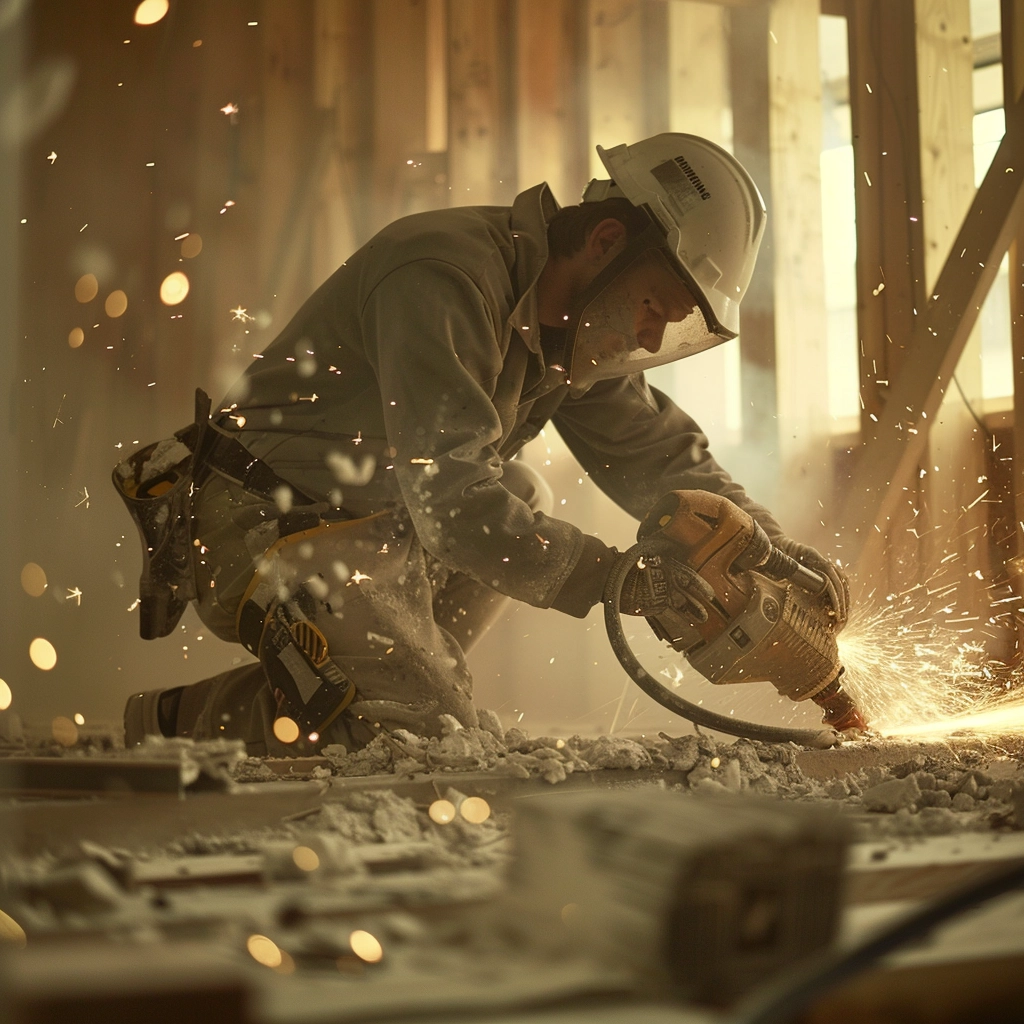
Top 5 Pneumatic Tools Safety Tips
Introduction
In the industrial sectors of construction, manufacturing, and automotive repair, pneumatic tools have become essential due to their efficiency and durability. These compressed air-powered tools, also known as air-powered hand tools, are utilized for a wide variety of tasks, ranging from precision work in assembly to heavy-duty demolition jobs. Despite their power and versatility, these tools come with inherent risks, making pneumatic tools safety a top priority for maintaining a secure work environment. This article will delve into the key safety protocols necessary for operating pneumatic tools safely, including the importance of maintenance, personal protective equipment (PPE), and proper training.
The Critical Importance of Safety
Ensuring safety while using pneumatic tools is of utmost importance. These tools operate using significant force, which, if not properly controlled, can lead to severe accidents. Hazards such as fractured blades, corroded parts, obstructions, and malfunctioning triggers can compromise both the performance of the tools and the safety of the operator. Additionally, the high-pressure air that powers pneumatic tools can be dangerous if mishandled. Understanding and implementing pneumatic tools safety protocols, including regular maintenance and proper handling, is essential to reduce the risk of injury.
Understanding the Risks
The risks associated with pneumatic tools can be extensive. Components such as blades, motors, and ball bearings may deteriorate over time, and inadequate air pressure or lubrication can lead to inefficiencies. Issues such as blocked or damaged rotors, cylinders, or springs can cause malfunctions, leading to uncontrolled tool operation—a common hazard when working with pneumatic equipment. These risks make it clear that pneumatic tools safety requires regular inspections and proactive maintenance to prevent accidents and ensure efficient performance.

Top 5 Pneumatic Tools Safety Tips
1. Regular Maintenance and Inspection
Consistently inspecting and maintaining pneumatic tools is a fundamental aspect of pneumatic tools safety. Prior to use, ensure all tool components are in optimal condition and immediately address any signs of wear or damage. Routine maintenance not only prevents accidents but also ensures peak performance. Always refer to the manufacturer's instructions to understand the specific maintenance needs of your pneumatic tools.
2. Utilize Proper Personal Protective Equipment (PPE)
Wearing the right PPE is crucial when operating pneumatic tools. Depending on the tool and the task, necessary protective gear may include safety glasses, gloves, ear protection, and respiratory masks. Eye protection is particularly important when working with pneumatic tools due to the potential for debris to be propelled by compressed air. Incorporating proper PPE is an integral part of pneumatic tools safety.
3. Ensure Adequate Training and Education
All operators should receive thorough training on the correct usage and maintenance of pneumatic tools. This includes understanding the hazards associated with these tools, learning proper lubrication techniques, and knowing how to respond in case of an emergency. Continuous education on pneumatic tools safety standards, and updates on new equipment, are vital to ensuring a safe working environment.
4. Be Aware of Common Mistakes
Common mistakes such as using damaged tools, ignoring safety features like clips, or failing to follow the manufacturer's guidelines can lead to accidents. Only use attachments that are rated for the pneumatic tool being used, and always follow pneumatic tools safety protocols to avoid unnecessary risks.
5. Comply with Safety Regulations and Industry Standards
Familiarize yourself with industry regulations, including those from organizations like the Occupational Safety and Health Administration (OSHA) and other relevant authorities. These guidelines help establish a safe working environment and reinforce the importance of pneumatic tools safety. Following proper air line installation procedures, including the use of regulators, lubricators, and air fuses, also plays a significant role in maintaining safety.
Conclusion
Pneumatic tools are invaluable across many industries, but their use requires a firm commitment to safety. By adhering to these top five safety tips—regular maintenance, proper PPE usage, comprehensive training, avoiding common mistakes, and complying with safety standards—operators can significantly reduce the risks associated with pneumatic tools. Remember that pneumatic tools safety is not just about meeting regulatory requirements; it's about safeguarding yourself and your colleagues. Always be mindful of potential trip hazards from air hoses and use warning signs to alert others of pneumatic tool usage.
For insights on How to Select the Top 3/4 Inch Air Impact Wrench for Your Workshop Needs, emphasizing the criticality of safety measures in pneumatic tool operation. Pneumatic tools safety should remain at the forefront of every operation.
Soartectools wishes you success in your endeavors.
