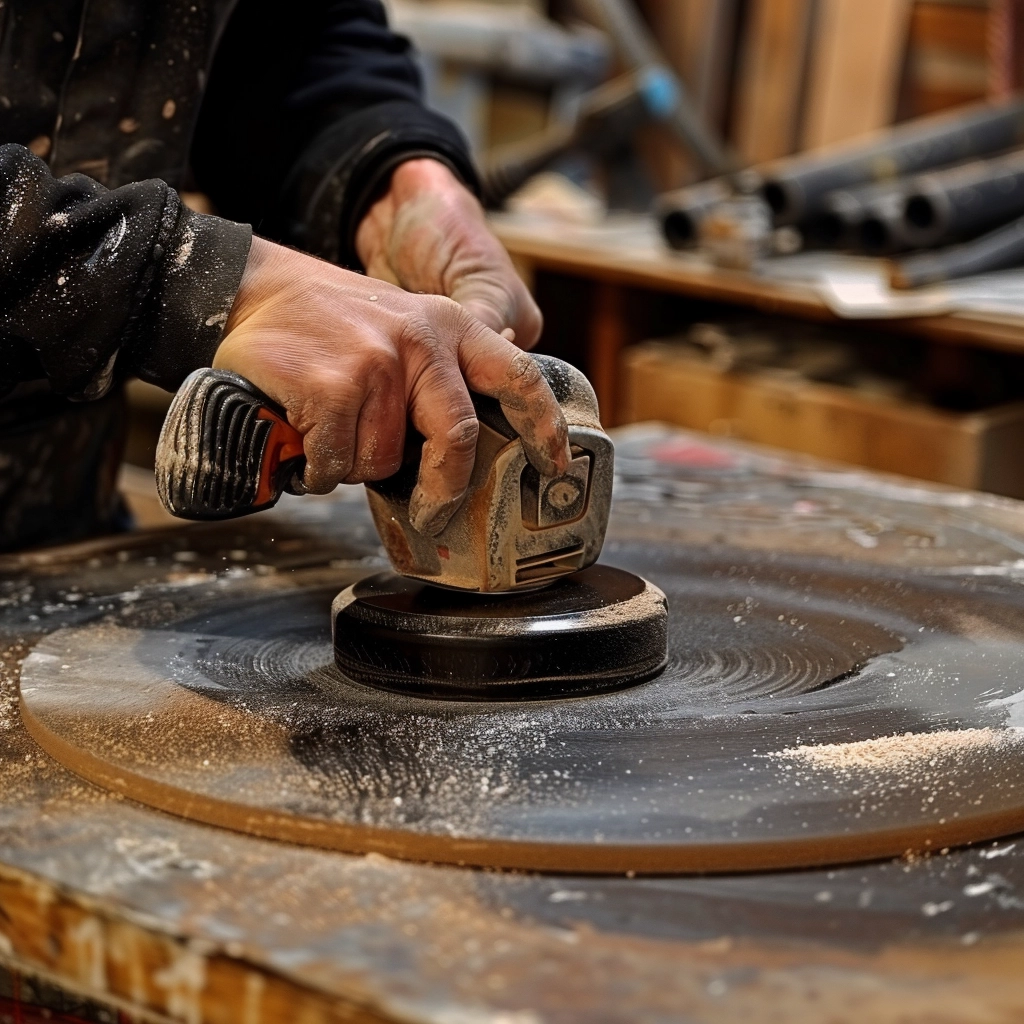
A Comprehensive Guide to Pneumatic Tools in Industrial Settings
Introduction: The Role of Pneumatic Tool in Modern Industry
In the realm of industrial machinery, efficiency and precision are paramount. Pneumatically powered tools, driven by compressed air, have emerged as crucial enablers in various industrial settings, known for their reliability, power, and versatility. This guide delves deep into the world of pneumatic tool, highlighting their role and the advantages of pneumatic systems in modern industrial manufacturing processes.
Understanding Pneumatic Tools: Basics and Components
Pneumatic tools, or air tools, leverage compressed air to drive operations, excelling in tasks such as drilling, grinding, and assembly. The principal components of a pneumatic system include an air compressor, the tool itself, and a network of hoses and connectors, making up a robust system tailored for industrial use. Understanding what pneumatics is reveals their efficiency and adaptability in various settings, showcasing examples of pneumatic systems where pneumatic tools get their power from compressed air through air hoses.
Key Applications: Where Pneumatic Tools Make a Difference
Assembly Line OperationsThese tools are pivotal in assembly lines, enhancing the speed and efficiency with which products are assembled, proving especially beneficial in automotive and electronics industries due to their precision and rapid operation. Their role in industrial manufacturing processes cannot be overstated, as pneumatic tools contribute significantly to productivity and quality.
Metalworking and MachiningOffering unmatched power and control for grinding, polishing, and cutting, pneumatic tools are indispensable in metalworking and machining, assisting in tasks that require high precision and consistent power. From die grinders to straight and air grinders, and even pneumatic sanders, these tools are crucial for effective material handling and removal.
Construction and CarpentryEnhancing productivity with pneumatic nail guns, staple guns, and drills, these tools are widely used for driving fasteners quickly and efficiently in construction and carpentry projects. Their application in woodworking demonstrates the versatility and efficiency of air tools, showcasing how pneumatic drills and air drills become essential power tools in these settings.
Exploring the Advantages: Why Choose Pneumatic Over Electric?
Pneumatic tools boast a high power-to-weight ratio, providing significant power without the heft, which reduces operator fatigue and enhances tool control. Moreover, unlike electric tools, which may suffer from power fluctuations, pneumatic tools ensure consistent power output and are notably durable, capable of withstanding harsh industrial environments. This advantage of pneumatic systems makes them a preferred choice in various sectors, highlighting their robustness.
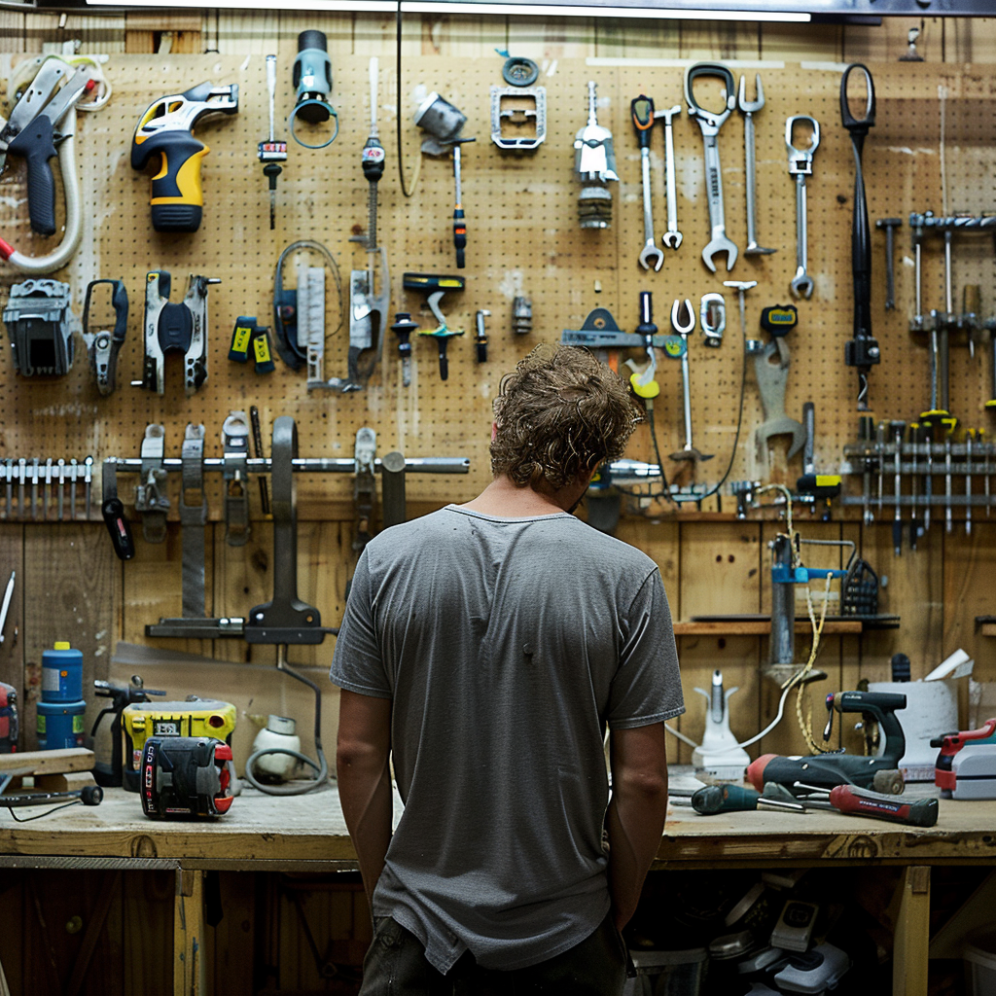
Maintenance Essentials: Keeping Your Tools in Top Shape
Regular lubrication with compatible oils is crucial for the smooth operation and longevity of pneumatic tools. Ensuring that the compressed air is clean and dry is equally important, as moisture and contaminants can severely impact tool performance. Proper maintenance is key to the durability of pneumatic equipment, ensuring they operate at peak efficiency.
Best Practices: Ensuring Safety and Efficiency
Adhering to safety guidelines while using pneumatic tools is essential to maintain a safe working environment. Proper storage practices are also critical; tools should be stored in a clean, dry environment to prevent corrosion and ensure they are ready for use when needed. This approach ensures the longevity and reliability of pneumatic tools, making them a staple in safe industrial practices.
Case Studies: Pneumatic Tools in Action
Through real-world applications and success stories, this section demonstrates the efficiency and benefits of pneumatic tools in various sectors, providing insights into their practical advantages and operational excellence. The industrial applications of these tools highlight their significant impact on productivity and quality, showcasing their versatility across different fields.
Choosing the Right Tools: A Buyer’s Guide
This segment provides guidance on selecting the right pneumatic tools for specific industrial applications, taking into consideration factors such as tool type, required power output, and the specific needs of the task at hand. Understanding these factors is crucial for optimizing performance and achieving desired outcomes in industrial settings, ensuring the right pneumatic tools are chosen for the job.
Future Trends: Innovations in Pneumatic Tool Technology
The pneumatic tool industry is on an upward trajectory, with continuous innovations aimed at boosting efficiency, slashing energy consumption, and elevating user safety through sustainable practices. This section explores the latest technological breakthroughs and the future prospects for pneumatic tools and pneumatic energy solutions in industrial environments, underscoring their pivotal role in advancing energy efficiency.
Conclusion: Maximizing Industrial Productivity with Pneumatic Tools
Pneumatic tools represent more than just a fleeting trend; they are a significant boost to industrial productivity and a fundamental element of industrial manufacturing. By adopting these tools and adhering to best practices for their usage and maintenance, industries can achieve high efficiency and extend the lifespan of their equipment, positioning pneumatic tools as a smart investment for contemporary industrial operations.
Soartectools wish you all luck. Tap to learn more our product.
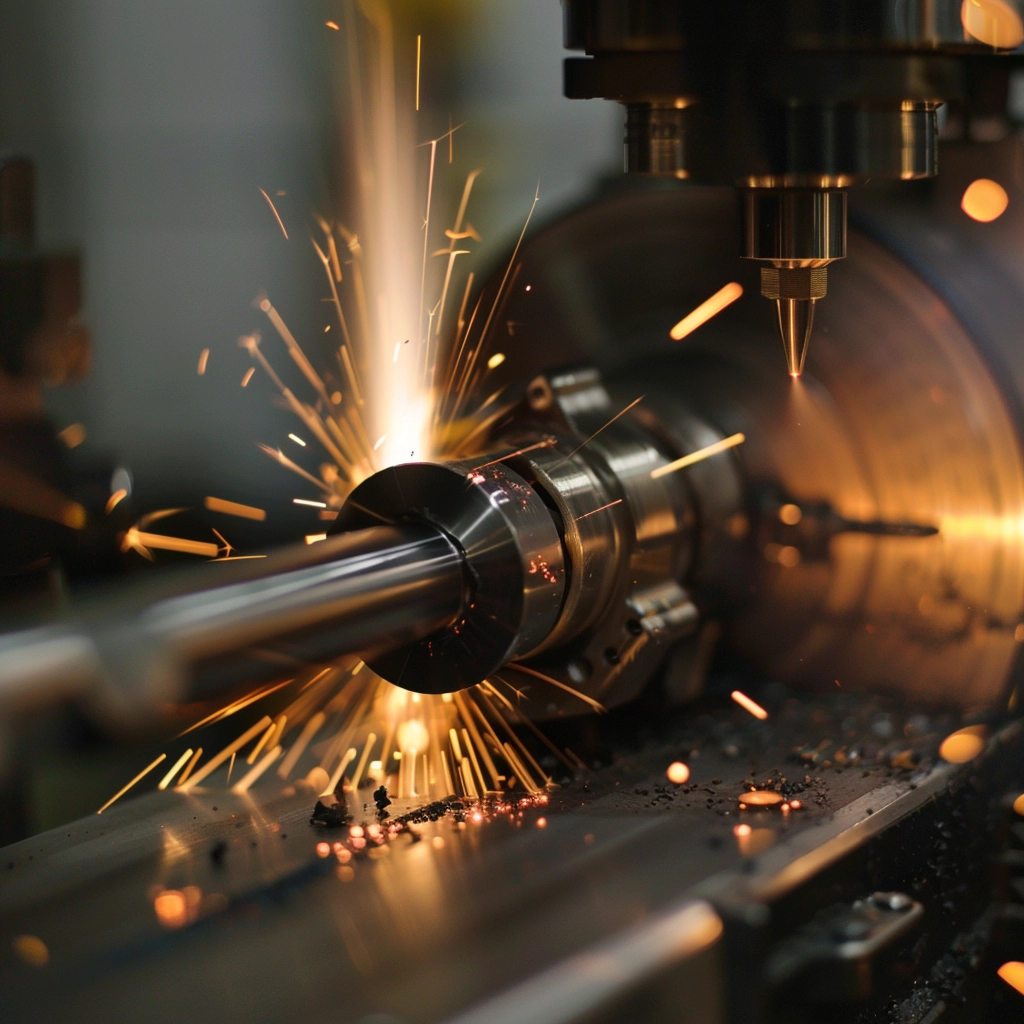