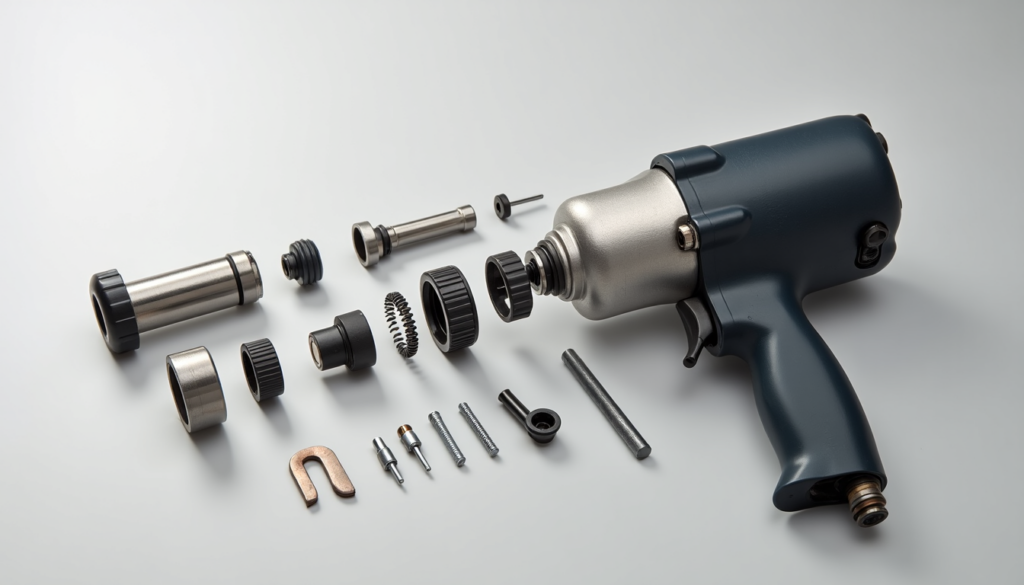
A 1/2″ air impact wrench has several critical parts that we’ll get into here. The twin hammer mechanism, blade with spring assembly, and air inlet system are the foundations of this tool. Users need to learn about specific requirements like air consumption, free speed, and max torque ratings. The tool needs proper air pressure to work right. A detailed air tool parts breakdown shows everything in the impact mechanism diagram that gives a clear explanation of the tool’s structure and how it works.
Overview of 1/2″ Air Impact Wrench Parts Diagram
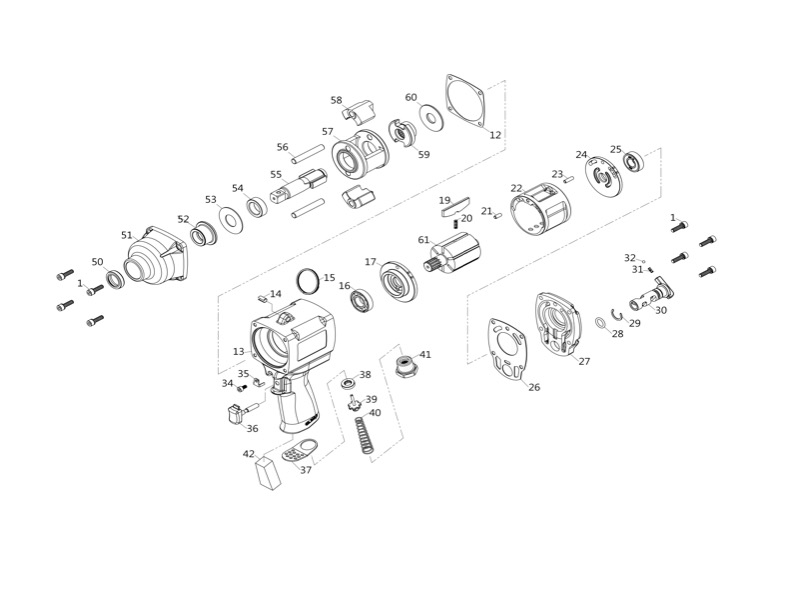
This Soartec 1/2″ air impact wrench WS-208 features a twin hammer mechanism that delivers reliable power and durability. The tool’s pressure-feed lubrication system ensures dependable performance and a longer operational life.
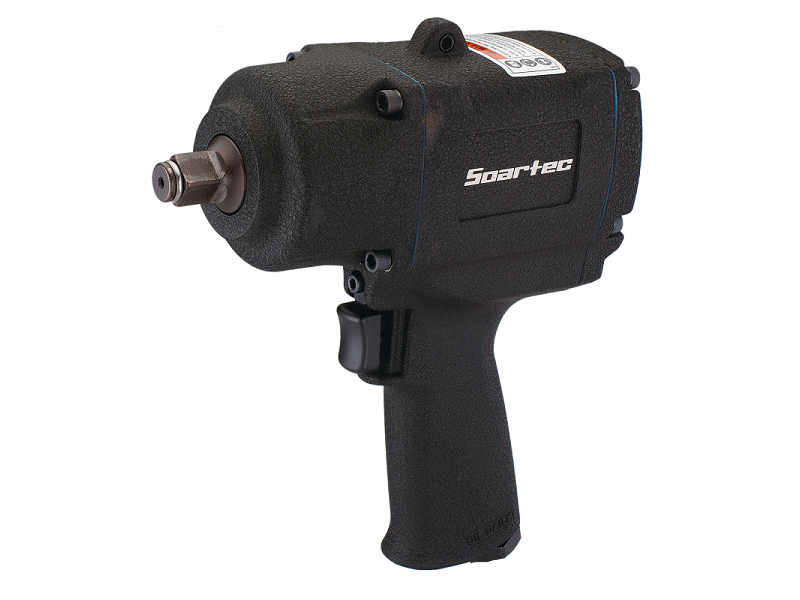
Key components of the system include:
- Twin hammer impact mechanism with heat-treated components
- Variable speed control with 6 position power regulator
- Solid steel front-end body construction
- Blade with spring mounted to prevent dead-lock or power-less problem
- Contoured sure-grip handle with vibration reduction
The technical specifications demonstrate the tool’s impressive capabilities:
Specification Value | |
Free Speed | 7,500 RPM |
Maximum Torque | 960 ft-lb |
Air Consumption | 17 CFM |
Sound Level | 101.8 dB(A) |
Weight | 5.78 lb |
The twin power motor design uses compressed air to generate substantial torque with precise control. The cushioned grip handle helps reduce operator fatigue during long periods of use. The robust front-end construction shields internal components. Users can make precise air impact wrench torque adjustments up to 560 ft-lbs with the built-in power regulator, making this tool suitable for different jobs.
It’s worth noting that while we’re focusing on the 1/2″ air impact wrench, there are other sizes available such as the 1″ impact wrench, 3/8″ impact wrench, and mini impact wrench, each designed for specific applications and torque requirements.
Assembly and Disassembly Guide
Air impact wrenches need proper maintenance and assembly to work at their best. Technicians must follow these safety protocols before they start any work:
- Wear appropriate safety glasses and hearing protection
- Ensure adequate workspace lighting
- Disconnect air supply completely
- Have proper tools readily available
- Maintain clean work surface
The disassembly process works best with these steps:
- Remove the hammer case assembly
- Extract the motor housing carefully
- Remove rotor assembly and vanes
- Separate the impact mechanism components
- Document placement of small parts
Technicians should check all parts for wear patterns during disassembly. The impact mechanism and rotor assembly need special attention. Performance drops by a lot when old lubricant builds up, so clean everything thoroughly.
For a comprehensive guide on this process, refer to the air wrench disassembly instructions or the impact wrench repair manual specific to your model, such as the WS-220 series or WS-208 series.
The reassembly needs the right type of lubrication. Use specialized grease on the impact mechanism and air tool oil for the motor assembly. Add 4-6 drops of oil to the air inlet before operation. Check the hammer mechanism regularly and replace worn parts to keep the tool working at its best. An air tool rebuild kit can be helpful for this maintenance process.
Conclusion
Air impact wrenches showcase advanced engineering. Their twin hammer mechanisms and precision-engineered components work naturally together. These powerful tools deliver exceptional performance through well-designed systems that include pressure-feed lubrication and variable speed control mechanisms. Professional technicians can improve tool efficiency and ensure safe operation in demanding applications by understanding these internal workings.
Regular maintenance is the life-blood of reliable air impact wrench performance. Tool life extends substantially when technicians inspect critical components, apply proper lubrication, and follow careful assembly procedures. Following detailed maintenance protocols helps protect the investment and ensures consistent, powerful performance in critical automotive and industrial applications. For ongoing maintenance, it’s crucial to refer to an impact wrench troubleshooting guide and pay attention to air impact wrench lubrication points to keep the tool in optimal condition.
Air impact wrenches are indispensable tools in any mechanic’s arsenal, available in various sizes to suit different tasks. The 3/8″ air impact wrench is perfect for precision work, while the 3/4″ model strikes a balance between power and versatility, making it a top choice for many workshops. For heavy-duty applications, the 1″ air impact gun stands out with its unmatched strength. Understanding the unique benefits of each size ensures you choose the right tool for your needs, whether it’s for delicate adjustments or industrial-level performance.
FAQs
What is the recommended hose size for a 1/2″ air impact wrench ?
To ensure a 1/2″ impact wrench operates at full capacity, it is advisable to use an air hose that is at least 10mm in diameter, as this size can handle the higher CFM requirements of the tool. This min hose size is crucial for maintaining proper air flow.
What type of air compressor is suitable for a 1/2” air impact wrench?
The size of the compressor needed for a 1/2-inch impact wrench depends on the specific requirements of the tool, including its CFM (Cubic Feet per Minute) and PSI (Pounds per Square Inch) ratings. For most 1/2″ impact wrenches, a compressor capable of delivering at least 5 CFM at 90 PSI is recommended.
What is the optimal PSI for operating an air impact wrench?
Most air impact wrenches are designed to function best at around 90 PSI (6.3 bars). It’s important to use an air regulator to accurately monitor and adjust the pressure when the wrench is connected to the compressor. Soartec aims to develop a full range of models that operate exclusively at 90 PSI air pressure.
Why might an air impact wrench not perform optimally?
A common reason for reduced performance in air impact wrenches is inadequate maintenance. Regular lubrication (SAE#10) can significantly improve tool performance by reducing internal friction and preventing water damage. Other factors could include worn internal components, improper air supply, or issues with the impact socket retention system. Consulting a pneumatic tool schematic drawing or an air impact gun exploded view can help identify potential problem areas.
What are the differences between various impact wrench types?
Impact wrenches come in various sizes and designs to suit different applications. For instance, a 1-1/2″ impact wrench is typically used for heavy-duty industrial applications, while a D-handle impact wrench offers improved ergonomics for extended use. Composite impact wrenches are lighter and provide better insulation against cold and vibration. The choice between a standard anvil and a 2″ anvil depends on the specific job requirements and socket compatibility.