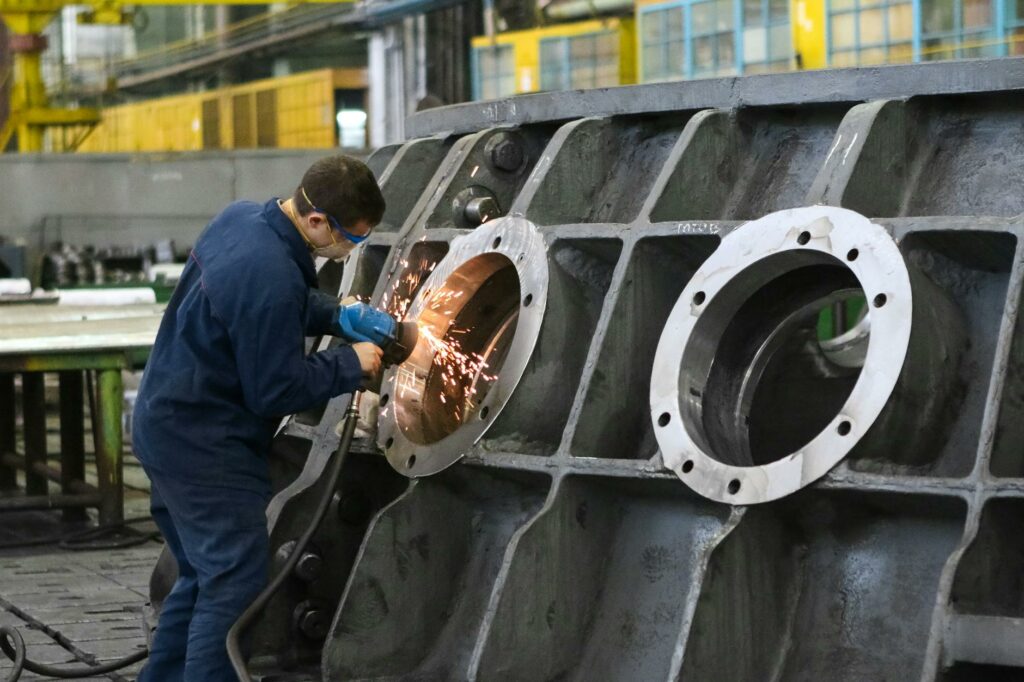
In the dynamic realm of metal fabrication, precision and efficiency are paramount. With their unrivaled power and versatility, pneumatic grinders have emerged as indispensable allies for professionals seeking to conquer even the most demanding projects. These air-powered marvels harness the potent force of compressed air, transforming it into a symphony of controlled abrasion and meticulous material removal.
From automotive repair and bodywork to construction and metalworking, professional-grade pneumatic grinders for metal fabrication have proven their mettle time and again. Their ability to effortlessly shape, refine, and sculpt metal surfaces with unparalleled precision sets them apart as true workhorses in the industry.
In this comprehensive guide, we delve into the realm of top-tier professional-grade pneumatic grinders for metal fabrication, unveiling their intricate workings, diverse applications, and the key factors that separate the exceptional from the ordinary. Prepare to embark on a journey through the pinnacle of pneumatic grinding technology, where power, precision, and efficiency converge to redefine the boundaries of metal mastery.
The Pneumatic Powerhouse: Harnessing the Force of Compressed Air
At the core of every professional-grade pneumatic grinder for metal fabrication lies a remarkable feat of engineering: the ability to harness the immense power of compressed air. This ingenious design principle sets pneumatic grinders apart from their electric counterparts, bestowing them with a unique set of advantages that have captivated the hearts and minds of metal fabrication professionals worldwide.
The Science Behind Pneumatic Power
Pneumatic grinders derive their unrivaled strength from the conversion of compressed air into rotational force. This process is facilitated by a sophisticated internal mechanism that channels the high-pressure air through a series of precisely engineered vanes or rotors, generating a torque-laden spinning motion.
The beauty of this system lies in its simplicity and efficiency. Unlike electric motors, which rely on complex electrical circuitry and intricate components, pneumatic grinders operate on the fundamental principles of fluid dynamics and kinetic energy transfer. This streamlined design not only enhances reliability and reduces maintenance requirements but also ensures a consistent and unwavering power delivery, even under the most demanding conditions.
Advantages of Pneumatic Power
Beyond their sheer force, professional-grade pneumatic grinders for metal fabrication offer a host of advantages that have solidified their reputation as industry leaders:
- Unparalleled Power-to-Weight Ratio: Pneumatic grinders boast an exceptional power-to-weight ratio, delivering immense grinding capabilities while remaining remarkably lightweight and maneuverable. This attribute is particularly valuable in metal fabrication, where prolonged use can lead to operator fatigue, compromising precision and safety.
- Spark-Free Operation: Unlike their electric counterparts, pneumatic grinders generate no electrical sparks during operation, making them inherently safer for use in hazardous environments or in the presence of flammable materials.
- Consistent Performance: The power output of pneumatic grinders remains consistent throughout their operational cycle, ensuring uniform material removal and a smoother overall grinding experience.
- Reduced Maintenance: With fewer moving parts and a simpler internal mechanism, pneumatic grinders require less frequent maintenance and servicing, minimizing downtime and maximizing productivity.
- Cooler Operation: The absence of electrical resistance and the continuous flow of compressed air help dissipate heat more effectively, allowing pneumatic grinders to operate at cooler temperatures and reducing the risk of overheating or thermal damage.
As you delve deeper into the world of professional-grade pneumatic grinders for metal fabrication, you’ll soon discover that their power and efficiency are only the beginning. These versatile tools offer a multitude of specialized features and configurations tailored to meet the diverse needs of the metal fabrication industry.
Exploring the Versatile Range of Pneumatic Grinders
The realm of professional-grade pneumatic grinders for metal fabrication is a vast and diverse one, encompassing a wide array of tools designed to tackle specific tasks and material types. From compact die grinders for intricate detailing to robust angle grinders for aggressive material removal, each tool in this arsenal serves a unique purpose, empowering professionals to achieve unparalleled results with precision and efficiency.
Die Grinders: Precision and Finesse Incarnate
When it comes to intricate metalworking tasks that demand surgical accuracy, die grinders reign supreme. These compact and lightweight pneumatic tools are engineered for precision, allowing operators to navigate even the tightest spaces with ease.
Die grinders excel in applications such as deburring, porting, and intricate surface finishing, where the slightest deviation can compromise the integrity of the final product. Their high-speed rotating spindles, coupled with a vast array of interchangeable accessories like carbide burrs, grinding stones, and sanding drums, enable unparalleled control and finesse.
Whether you’re a skilled tool and die maker, an automotive technician, or a metalworking artisan, die grinders are an indispensable ally, empowering you to bring your vision to life with unmatched precision and attention to detail.
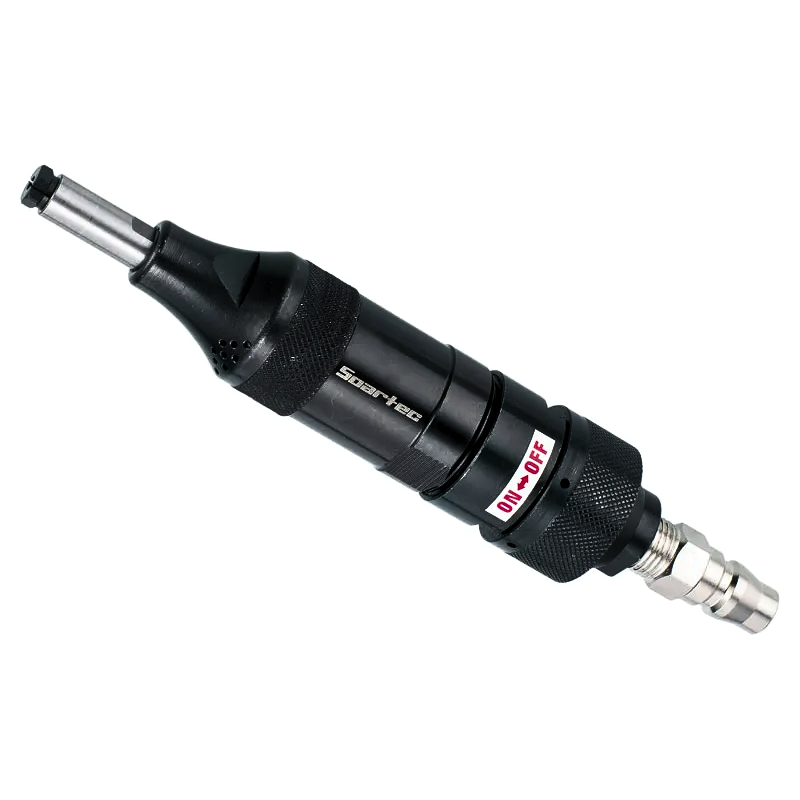
Angle Grinders: Brute Force and Versatility Combined
On the opposite end of the spectrum lie angle grinders, the workhorses of the pneumatic grinding world. These robust tools are designed to tackle the most demanding material removal tasks with unrelenting power and efficiency.
Angle grinders derive their name from their distinctive angled grinding disc configuration, which allows for aggressive cutting, grinding, and surface preparation on a wide range of materials, including metals, concrete, and masonry.
What sets professional-grade pneumatic grinders for metal fabrication</primary keyword> apart is their exceptional power-to-weight ratio and ergonomic design. Even the most compact models can deliver an impressive amount of torque, enabling effortless material removal while minimizing operator fatigue.
From automotive bodywork and repair to heavy-duty construction projects, angle grinders are the go-to choice for professionals seeking a versatile and powerful tool that can handle virtually any task thrown their way.
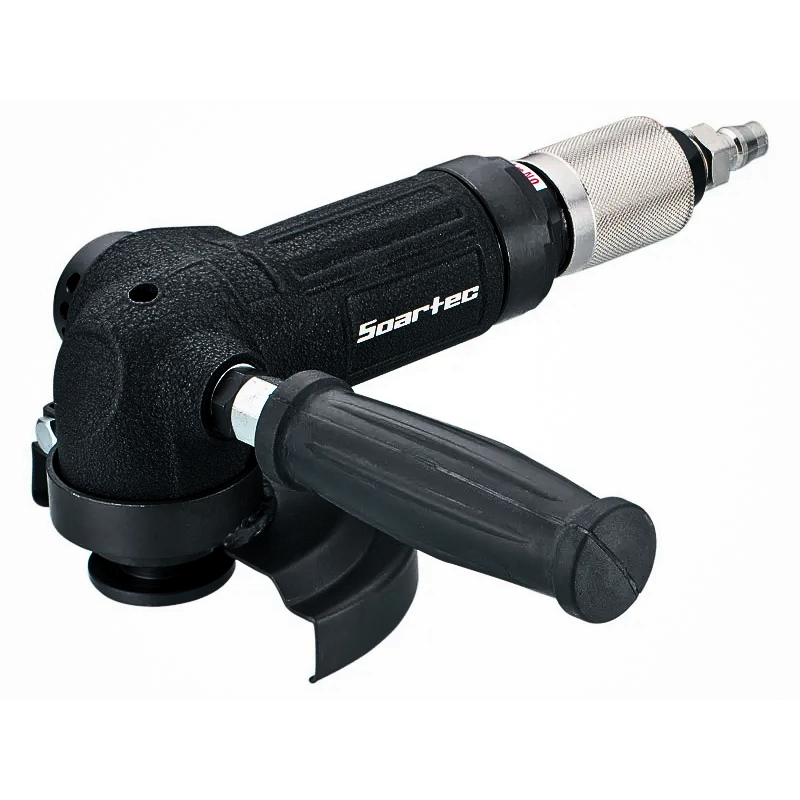
Straight Grinders: The Perfect Balance of Power and Precision
Bridging the gap between die grinders and angle grinders, straight grinders offer a harmonious blend of power and precision. These pneumatic tools feature a straight, in-line design that allows for precise control and maneuverability, making them ideal for a wide range of applications.
Straight grinders excel in tasks such as surface finishing, deburring, and weld preparation, where a delicate touch and controlled material removal are paramount. Their compact size and ergonomic design make them well-suited for working in confined spaces or on intricate components.
Whether you’re a skilled metalworker, a maintenance technician, or a fabricator, straight grinders provide the perfect balance of power and precision, enabling you to tackle even the most demanding projects with confidence and ease.
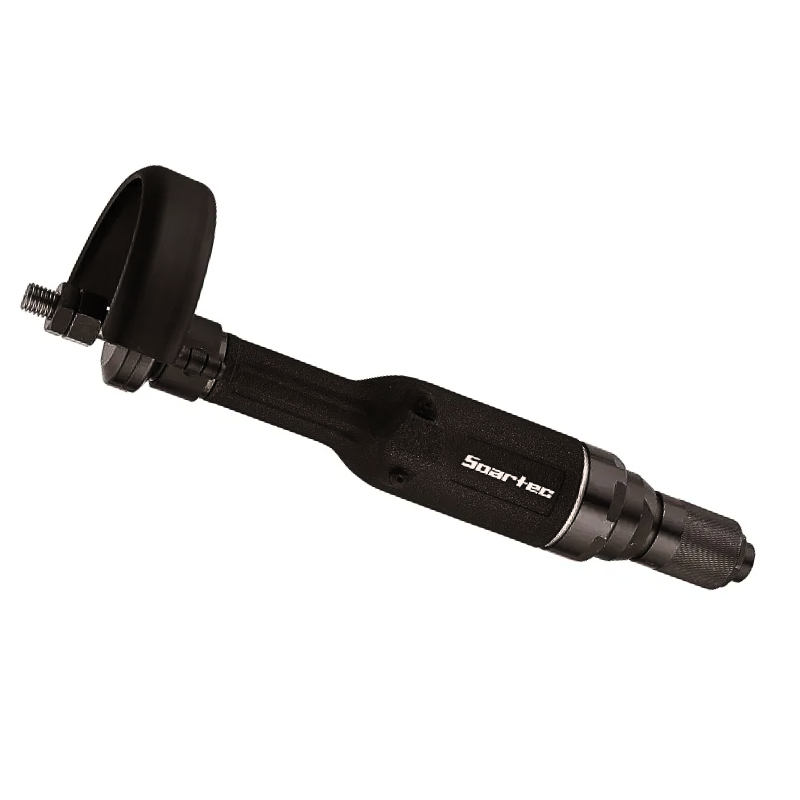
Belt Grinders: Shaping Metal with Finesse
For those seeking a more refined approach to metal shaping and finishing, belt grinders offer a unique solution. These specialized pneumatic tools utilize a continuous loop of abrasive belts to precisely grind, smooth, and contour metal surfaces.
Belt grinders are particularly well-suited for tasks such as sharpening tools, shaping and contouring metal components, and achieving precise surface finishes. Their adjustable tool rests and variable speed settings allow for precise control over the material removal process, ensuring consistent and repeatable results.
Whether you’re a knifemaker, a sculptor, or a metalworking artisan, belt grinders provide the finesse and control necessary to bring your vision to life, transforming raw metal into works of art with unparalleled precision and artistry.
Bench Grinders: Versatility at Your Workbench
No metalworking workshop would be complete without a trusty bench grinder. These stationary pneumatic tools are designed to be mounted securely on a workbench or dedicated stand, providing a stable and reliable platform for a wide range of grinding and sharpening tasks.
Bench grinders typically feature two grinding wheels of varying grit sizes, allowing for both coarse and fine grinding operations. Their adjustable tool rests and eye shields ensure precise control and operator safety, making them ideal for tasks such as tool sharpening, deburring, and general-purpose grinding.
Whether you’re a hobbyist, a DIYer, or a professional metalworker, a bench grinder is an essential addition to your workshop, offering versatility, convenience, and the peace of mind that comes with a reliable and time-tested tool.
With such a diverse array of pneumatic grinders at your disposal, the possibilities for metal fabrication are truly limitless. However, to truly harness the power and potential of these tools, it’s crucial to understand the factors that separate the exceptional from the ordinary.
Separating the Exceptional from the Ordinary: Key Factors to Consider
In the competitive landscape of professional-grade pneumatic grinders for metal fabrication, not all tools are created equal. While some may boast impressive specifications and flashy features, true excellence lies in the seamless integration of performance, ergonomics, and durability. By understanding the key factors that separate the exceptional from the ordinary, you can make informed decisions and invest in tools that will not only meet but exceed your expectations.
Power and Performance: The Engine that Drives Productivity
At the heart of every professional-grade pneumatic grinder for metal fabrication lies its power and performance capabilities. These attributes are intrinsically linked to the tool’s ability to efficiently convert compressed air into rotational force, enabling aggressive material removal and unparalleled productivity.
When evaluating power and performance, consider factors such as:
- Air Consumption: The amount of compressed air consumed by the tool, typically measured in cubic feet per minute (CFM) or liters per minute (LPM). Higher air consumption generally translates to greater power output.
- Operating Speed: The rotational speed of the grinding accessory, measured in revolutions per minute (RPM). Higher operating speeds allow for faster material removal and improved efficiency.
- Torque: The rotational force produced by the tool, measured in inch-pounds or newton-meters. Higher torque values enable the tool to maintain consistent performance even under heavy loads.
It’s essential to strike the right balance between power and performance, ensuring that the tool can handle your specific applications without compromising efficiency or operator comfort.
Ergonomics and Comfort: Enhancing Precision and Productivity
In the demanding world of metal fabrication, prolonged tool usage can lead to fatigue, compromising precision and productivity. This is where ergonomics and comfort play a crucial role, ensuring that operators can work efficiently and safely for extended periods without experiencing undue strain or discomfort.
When evaluating the ergonomics of professional-grade pneumatic grinders for metal fabrication</primary keyword>, consider factors such as:
- Weight and Balance: A well-balanced, lightweight design minimizes operator fatigue and improves control, reducing the risk of accidents or errors.
- Grip and Handling: Ergonomically designed handles and grips provide a secure and comfortable hold, enhancing precision and minimizing hand strain.
- Vibration Control: Advanced vibration dampening technologies help reduce the transmission of vibrations to the operator’s hands, minimizing fatigue and discomfort.
- Noise Reduction: Low-noise operation not only improves the working environment but also reduces operator fatigue and potential hearing damage.
By prioritizing ergonomics and comfort, you can ensure that your pneumatic grinders are not only powerful and efficient but also user-friendly, enabling you to maintain peak performance throughout even the most demanding projects.
Durability and Longevity: Investing in Long-Term Performance
In the demanding world of metal fabrication, tools are subjected to rigorous use and harsh operating conditions. Durability and longevity are paramount, as downtime and frequent tool replacements can significantly impact productivity and profitability.
When assessing the durability of professional-grade pneumatic grinders for metal fabrication, consider factors such as:
- Construction Materials: High-quality materials, such as composite housings, heat-treated gears, and precision-machined components, ensure long-lasting performance and resistance to wear and tear.
- Bearing and Lubrication Systems: Robust bearing systems and effective lubrication mechanisms minimize friction and wear, extending the tool’s lifespan and reducing maintenance requirements.
- Environmental Protection: Features such as sealed housings and moisture-resistant components protect the tool’s internal mechanisms from contamination and corrosion, ensuring reliable operation in even the harshest environments.
- Warranty and Service Support: A comprehensive warranty and readily available service and support from the manufacturer can provide peace of mind and minimize downtime in the event of any issues.
By investing in durable and long-lasting professional-grade pneumatic grinders for metal fabrication, you not only ensure consistent performance but also maximize the return on your investment, minimizing the need for frequent replacements and reducing overall operational costs.
Brand Reputation and Quality Assurance
In the competitive world of metal fabrication tools, brand reputation and quality assurance can be the deciding factors when choosing the right pneumatic grinder. Reputable manufacturers have earned their place in the industry through a commitment to excellence, innovation, and unwavering quality control.
When considering brand reputation and quality assurance, look for:
- Industry Recognition: Brands that are widely recognized and respected within the metal fabrication industry, known for their consistent quality and reliable performance.
- Manufacturing Standards: Adherence to stringent manufacturing standards and quality control processes, ensuring consistent product quality and performance.
- Customer Testimonials and Reviews: Positive customer feedback and reviews from industry professionals, attesting to the brand’s reliability, durability, and overall satisfaction.
- Certifications and Accreditations: Certifications from recognized bodies, such as ISO or ANSI, indicating that the brand meets or exceeds industry standards for quality and safety.
By aligning yourself with reputable brands that prioritize quality assurance, you can rest assured that your professional-grade pneumatic grinders for metal fabrication</primary keyword> will deliver the performance and reliability you expect, time and time again.
The Soartec Air Angle Grinder: A Paradigm of Professional-Grade Excellence
In the ever-evolving landscape of professional-grade pneumatic grinders for metal fabrication, one brand has consistently stood out as a beacon of innovation and excellence: Soartec. With a relentless pursuit of perfection and a deep understanding of the industry’s needs, Soartec has crafted a range of pneumatic tools that redefine what it means to be truly professional-grade.
The Soartec Air Angle Grinder is a shining example of this unwavering commitment to quality and performance. Engineered with meticulous attention to detail, this pneumatic powerhouse combines cutting-edge technology with ergonomic design, delivering unparalleled results in a package that epitomizes comfort and ease of use.
Unrivaled Power and Performance
At the heart of the Soartec Air Angle Grinder lies a meticulously engineered pneumatic motor, designed to harness the full potential of compressed air. With an exceptional power-to-weight ratio, this tool effortlessly tackles even the most demanding material removal tasks, delivering unrivaled performance and productivity.
The integrated internal governor optimizes speed under load, ensuring a consistent and efficient rate of material removal throughout the entire operation. This feature not only enhances productivity but also minimizes the risk of overloading or stalling, providing operators with a smooth and seamless grinding experience.
Ergonomic Excellence and Operator Comfort
While power and performance are undoubtedly crucial, the Soartec Air Angle Grinder also excels in ergonomics and operator comfort. Engineered with a lightweight composite housing and an improved grip design, this tool minimizes fatigue and strain, even during prolonged periods of operation.
The ergonomic design extends beyond just the grip, with strategically placed air inlets and exhaust ports that direct airflow away from the operator, reducing noise and improving overall comfort. Additionally, the tool’s low-vibration operation further enhances user experience, minimizing hand and arm fatigue.
Versatility and Adaptability
One of the hallmarks of the Soartec Air Angle Grinder is its versatility and adaptability across a wide range of industries and applications. From automotive repair and bodywork to construction and metal fabrication, this tool showcases its prowess with equal aplomb.
The ability to accept a diverse range of grinding accessories, including cutting discs, grinding wheels, and wire brushes, further expands the tool’s capabilities, allowing operators to tackle a multitude of tasks with a single, reliable solution.
Durability and Longevity You Can Trust
In the demanding world of metal fabrication, durability and longevity are non-negotiable. The Soartec Air Angle Grinder delivers on this front with its robust construction and meticulous attention to detail.
The built-in lubricating wick ensures that the angle gear set remains well-lubricated, maximizing the longevity of the bevel and pinion gear set. This innovative feature not only enhances the tool’s lifespan but also minimizes maintenance requirements, reducing downtime and maximizing productivity.
Additionally, the So artec Air Angle Grinder’s composite housing and precision-machined components are designed to withstand the rigors of demanding applications, ensuring reliable performance and minimizing the need for frequent replacements.
Unwavering Brand Reputation and Quality Assurance
Behind the Soartec Air Angle Grinder stands a brand with an unwavering reputation for quality and excellence. Soartec’s commitment to stringent manufacturing standards and rigorous quality control processes ensures that every tool that leaves their facility meets the highest industry benchmarks.
This dedication to quality is further bolstered by Soartec’s industry recognition and positive customer testimonials, solidifying their position as a trusted name in the realm of professional-grade pneumatic tools.
With the Soartec Air Angle Grinder, metal fabrication professionals can confidently tackle any project, secure in the knowledge that they are wielding a tool that embodies the pinnacle of power, precision, and reliability.
Construction and Metalworking
In the construction and metalworking industries, professional-grade pneumatic grinders for metal fabrication are invaluable tools for a wide range of applications, from heavy-duty material removal to precision finishing.
Weld Preparation and Finishing
Proper weld preparation and finishing are essential for ensuring the structural integrity and aesthetic appeal of metal fabrications. Pneumatic grinders play a vital role in this process, allowing operators to efficiently remove excess material, prepare joint surfaces, and smooth out weld beads.
Angle grinders equipped with abrasive discs or grinding wheels can quickly remove excess weld material, while die grinders and straight grinders provide the precision and control necessary for intricate weld finishing and deburring.
Metal Shaping and Fabrication
In the realm of metal shaping and fabrication, pneumatic grinders are versatile tools that enable precise material removal and shaping. From creating intricate profiles and contours to achieving desired surface finishes, these tools offer unparalleled control and precision.
Belt grinders, in particular, excel in tasks such as sharpening tools, shaping metal components, and achieving precise surface finishes. Their adjustable tool rests and variable speed settings allow for precise control over the material removal process, enabling operators to bring their visions to life with unmatched accuracy.
Maintenance and Repair
In addition to their applications in fabrication and construction, professional-grade pneumatic grinders for metal fabrication are invaluable tools for maintenance and repair tasks across various industries.
From removing rust and surface contaminants to deburring and smoothing metal surfaces, pneumatic grinders offer a versatile and efficient solution. Their ability to access hard-to-reach areas and their portability make them ideal for on-site maintenance and repair operations, minimizing downtime and maximizing productivity.
Best Practices for Safe and Effective Operation
While professional-grade pneumatic grinders for metal fabrication are powerful and versatile tools, their safe and effective operation requires adherence to best practices and proper safety protocols.
Personal Protective Equipment (PPE)
The use of appropriate personal protective equipment (PPE) is crucial when operating pneumatic grinders. This includes safety glasses or face shields to protect against flying debris, hearing protection to mitigate noise exposure, and sturdy gloves to prevent hand injuries.
Additionally, operators should wear appropriate clothing that covers exposed skin and avoid loose-fitting garments that could become entangled in the rotating accessories.
Proper Tool Setup and Inspection
Before each use, it is essential to inspect pneumatic grinders for any signs of damage or wear. This includes checking for cracks or damage to the housing, ensuring that all guards and safety features are in place, and verifying that the grinding accessories are securely mounted and in good condition.
Proper tool setup is also crucial, including adjusting tool rests and ensuring that the workpiece is securely clamped or supported to prevent movement during operation.
Controlled Material Removal
While pneumatic grinders are powerful tools, it is essential to exercise control and patience during material removal operations. Applying excessive force or pressure can not only damage the workpiece but also increase the risk of kickback or tool failure.
Operators should allow the tool to do the work, using controlled and consistent motions while maintaining the proper angle and pressure. Additionally, it is important to take breaks as needed to prevent overheating and excessive wear on the grinding accessories.
Dust and Debris Management
Many metal grinding operations generate significant amounts of dust and debris, which can pose health and safety risks if not properly managed. The use of appropriate dust collection systems or vacuum attachments is highly recommended to minimize exposure and maintain a clean and safe work environment.
In addition to dust management, it is important to keep the work area free from clutter and tripping hazards, ensuring a clear path for safe tool operation and movement.
By adhering to these best practices and prioritizing safety, metal fabrication professionals can unlock the full potential of professional-grade pneumatic grinders for metal fabrication, achieving exceptional results while minimizing the risk of accidents or injuries.
Sustainability and Environmental Considerations
In today’s world, sustainability and environmental responsibility are paramount considerations in virtually every industry, including metal fabrication. As professionals seek to minimize their environmental impact while maintaining productivity and efficiency, professional-grade pneumatic grinders for metal fabrication offer a compelling solution.
Energy Efficiency and Reduced Carbon Footprint
One of the key advantages of pneumatic grinders is their inherent energy efficiency. Unlike their electric counterparts, which rely on energy-intensive motors and power sources, pneumatic grinders harness the power of compressed air, a readily available and renewable resource.
This reliance on compressed air significantly reduces the energy consumption associated with metal grinding operations, translating into a lower carbon footprint and a more sustainable approach to metal fabrication.
Additionally, the absence of electric motors and the associated heat generation further contributes to energy efficiency, minimizing the need for additional cooling systems and reducing overall energy consumption.
Reduced Noise Pollution
Noise pollution is a significant concern in many industrial and manufacturing environments, impacting both worker health and the surrounding communities. Professional-grade pneumatic grinders for metal fabrication offer a distinct advantage in this regard, as they typically operate at lower noise levels compared to their electric counterparts.
This reduction in noise pollution not only improves the workplace but also minimizes the impact on surrounding areas, contributing to a more sustainable and environmentally responsible approach to metal fabrication.
Soartec’s Air Angle Grinder is actively committed to developing grinders that minimize noise. After rigorous product testing, the noise level is controlled between 85 to 95 dBA.
Recyclability and Waste Reduction
In the pursuit of sustainability, the recyclability and potential for waste reduction are crucial considerations. Pneumatic grinders, with their predominantly metal and composite construction, offer a distinct advantage in this regard.
Many of the components used in the manufacturing of these tools, such as the housings, gears, and spindles, can be easily recycled or repurposed, minimizing the environmental impact associated with their eventual disposal.
Furthermore, the longevity and durability of professional-grade pneumatic grinders for metal fabrication</primary keyword> contribute to waste reduction. By investing in high-quality tools designed for extended service life, professionals can minimize the need for frequent replacements, thereby reducing the amount of waste generated over time.
Responsible Manufacturing and Ethical Sourcing
As consumers become increasingly conscious of the environmental and social impacts of their purchasing decisions, responsible manufacturing and ethical sourcing practices have become paramount considerations.
Leading manufacturers of professional-grade pneumatic grinders for metal fabrication</secondary keyword> are committed to implementing sustainable and ethical practices throughout their supply chains. This includes sourcing raw materials from responsible and certified sources, minimizing waste and emissions during the manufacturing process, and ensuring fair labor practices and safe working conditions for their employees.
By aligning with manufacturers that prioritize responsible manufacturing and ethical sourcing, metal fabrication professionals can contribute to a more sustainable and socially responsible industry, while also ensuring that their tools meet the highest standards of quality and performance.
As the demand for sustainable and environmentally responsible practices continues to grow, professional-grade pneumatic grinders for metal fabrication emerge as a compelling solution, offering a powerful combination of performance, efficiency, and environmental stewardship.
The Future of Pneumatic Grinding Technology
In the ever-evolving world of metal fabrication, innovation and technological advancements are the driving forces that shape the future. As professional-grade pneumatic grinders for metal fabrication</primary keyword> continue to push the boundaries of performance and efficiency, exciting developments on the horizon promise to revolutionize the way we approach material removal and surface preparation.
Advancements in Pneumatic Motor Design
At the heart of every pneumatic grinder lies the pneumatic motor, a marvel of engineering that converts the power of compressed air into rotational force. Ongoing research and development in this area are paving the way for more efficient and powerful motor designs, promising increased material removal rates and improved energy efficiency.
Innovations such as advanced vane geometries, optimized air flow dynamics, and the integration of cutting-edge materials are poised to enhance the performance and longevity of pneumatic motors, enabling metal fabrication professionals to tackle even the most demanding projects with unparalleled ease.
Intelligent Speed and Torque Control
While pneumatic grinders have traditionally relied on manual speed and torque adjustments, the future holds the promise of intelligent, automated control systems. By integrating advanced sensors and computer-controlled mechanisms, these systems can dynamically adjust the tool’s speed and torque based on real-time feedback from the workpiece and operating conditions.
This level of intelligent control not only enhances precision and material removal efficiency but also contributes to improved operator safety and reduced tool wear. By automatically adjusting the tool’s performance to match the specific requirements of each task, professionals can achieve consistent and repeatable results while minimizing the risk of overloading or tool failure.
Integration of Internet of Things (IoT) and Predictive Maintenance
The Internet of Things (IoT) is rapidly transforming industries across the globe, and the world of professional-grade pneumatic grinders for metal fabrication</secondary keyword> is no exception. By integrating IoT technologies into these tools, manufacturers can unlock a wealth of data and insights that can drive further improvements in performance, efficiency, and maintenance practices.
Imagine a scenario where your pneumatic grinder is equipped with sensors that continuously monitor its performance, wear levels, and operating conditions. This data can be transmitted to a central system, enabling predictive maintenance algorithms to identify potential issues before they occur, minimizing downtime and maximizing tool lifespan.
Additionally, IoT connectivity can facilitate remote diagnostics and troubleshooting, enabling manufacturers and service providers to offer more proactive support and streamline maintenance processes.
Advancements in Abrasive Materials and Coatings
While pneumatic grinders have undergone significant technological advancements, the abrasive materials and coatings used in grinding accessories have also seen remarkable improvements. Ongoing research and development in this area are yielding new materials and formulations that offer enhanced durability, improved cutting performance, and increased resistance to wear and heat.
From advanced ceramic grains to diamond-like coatings, these innovations promise to extend the service life of grinding accessories, reducing the need for frequent replacements and minimizing operational costs. Additionally, these advancements may enable more efficient material removal rates, further enhancing the productivity and efficiency of pneumatic grinding operations.
As the future unfolds, the synergy between advancements in pneumatic grinder technology and innovations in abrasive materials and coatings promises to redefine the boundaries of what is possible in the world of metal fabrication.
Conclusion: Mastering the Art of Metal Fabrication
Selecting the right pneumatic grinder is crucial for achieving high-quality results in metal fabrication. The best professional-grade pneumatic grinders offer a combination of power, precision, and durability, making them indispensable tools for any serious metalworker. Soartec’s range of pneumatic grinders stands out for their innovative design, low noise levels, and exceptional performance. By considering the specific needs of your projects and understanding the unique features of each model, you can confidently choose a grinder that will enhance your productivity and craftsmanship. Invest in a reliable pneumatic grinder from Soartec, and experience the difference in your metal fabrication work.