Pneumatic drill gun has revolutionized the drilling industry, offering unprecedented power and precision for a wide range of applications. These versatile tools harness compressed air to deliver high torque and rapid drilling speeds, making them indispensable in construction, manufacturing, and maintenance sectors. From compact pistol-grip air drills to heavy-duty models, pneumatic drill guns cater to diverse needs and materials.
This comprehensive guide delves into the world of pneumatic drill guns, exploring their mechanics, types, and advantages. Readers will gain insights into selecting the right tool for specific tasks, maintaining equipment for optimal performance, and adhering to safety protocols. By understanding the nuances of these powerful devices, professionals can enhance their efficiency and tackle drilling projects with confidence.
Understanding Pneumatic Drill Guns
What is a Pneumatic Drill Gun?
A pneumatic drill gun is a handheld air-powered tool designed to drill holes or break hard surfaces like rock, concrete, and roads. These versatile devices harness compressed air pressure to deliver high torque and rapid drilling speeds. Pneumatic drill guns fall under ISO 11148-3:2012 standards and are known for their efficiency, capacity, and functionality in various industrial applications.
How Pneumatic Drill Guns Work
The operation of a pneumatic drill gun relies on compressed air as its power source. When an operator presses the handle, compressed air flows through a spring-loaded valve into the tool. Inside, a network of tubes directs the air to a heavy piledriver. The high-pressure air forces the piledriver down, causing it to pound into the drill bit and smash it into the ground. A valve then flips, changing the air circulation direction, which moves the piledriver back up. This process repeats rapidly, with the piledriver hitting the drill bit about 25 times per second, resulting in 1500 impacts per minute.
Key Components of Pneumatic Drill Guns
A typical pneumatic drill gun consists of several essential parts:
- Outer casing and handle
- Air inlet and outlet valves
- Internal network of tubes
- Piledriver
- Changeable drill bit
The heart of the tool is its air motor, which includes a rotor, rotor blades (or vanes), cylinder, upper and lower plates, and bearings. These components work together to convert compressed air into mechanical energy. The planetary gear system plays a crucial role in reducing speed while increasing torque, ensuring the tool maintains power during operation. The chuck allows for fitting different sizes of drill bits and accessories, making pneumatic drill guns adaptable to various tasks.
Types of Pneumatic Drill Guns
Straight Air Drills
Straight air drills are versatile tools designed for precision drilling in various materials. These pneumatic drill guns offer high torque and rapid drilling speeds, making them ideal for industrial production and intensive duty applications. Straight air drills come in different sizes, with drilling capacities ranging from 1/4″ to 1/2″. They typically operate at speeds between 300 and 2,500 RPM, catering to diverse drilling needs.
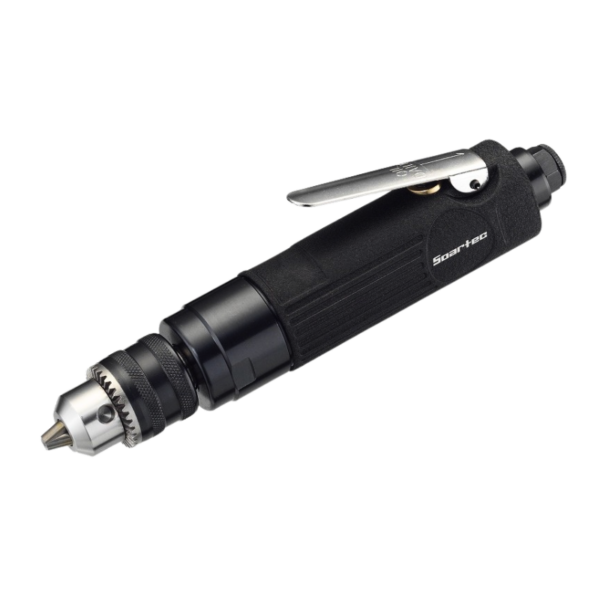
Air Straight Drill 3/8″
Angle Air Drills & Pistol Grip Air Drills
Angle air drills and pistol grip air drills are designed for working in tight spaces and awkward angles. Angle drills come in 45° and 90° configurations, allowing access to hard-to-reach areas. Pistol grip air drills offer enhanced operator comfort with their ergonomic design. These types of pneumatic drill guns are popular in body shops and general maintenance applications.
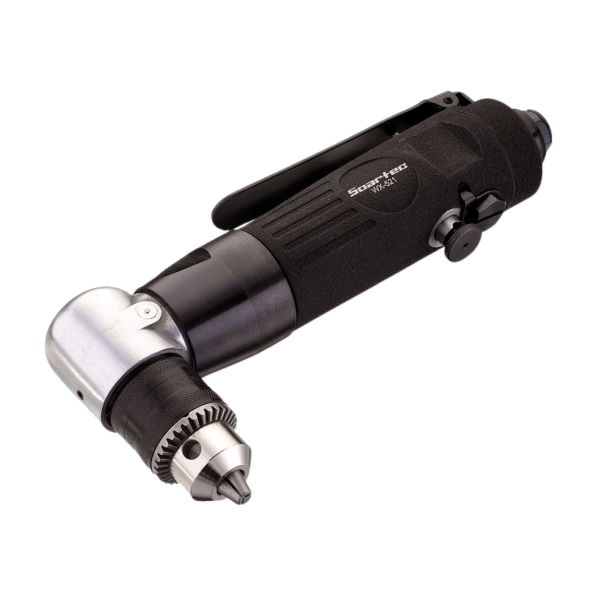
Reversible Air Drills
Reversible air drills provide the flexibility to drill in both forward and reverse directions. This feature is particularly useful for removing stuck drill bits or tapping operations. Reversible models are available in various sizes and configurations, including straight, angle, and pistol grip designs.
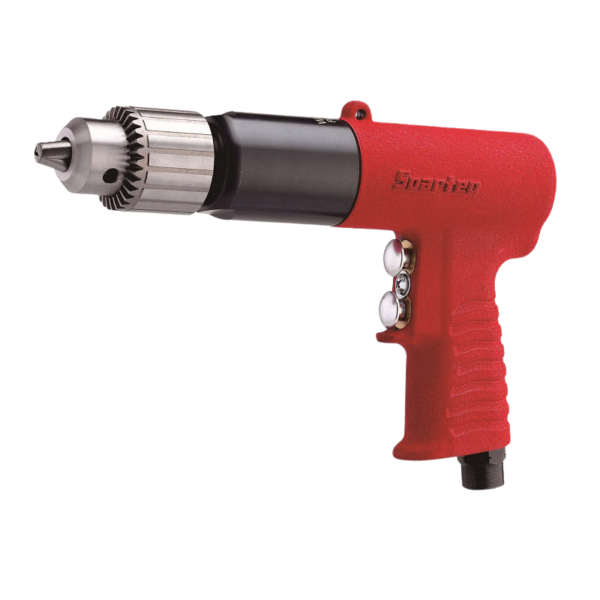
Composite Air Drills
Composite air drills are lightweight and durable, offering reduced operator fatigue during extended use. These pneumatic drill guns often feature oil-free motors, making them suitable for environments where oil contamination is a concern. Composite models typically have excellent power-to-weight ratios, enhancing productivity in industrial settings.
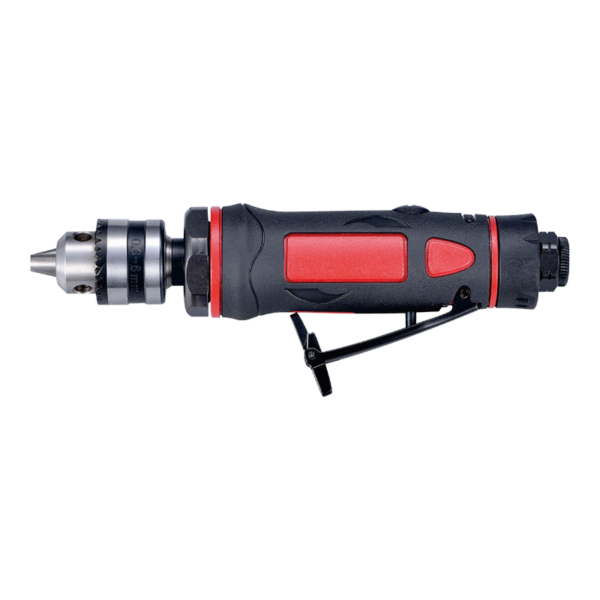
Air Tapping Drills
Air tapping drills are specialized pneumatic tools designed for creating threaded holes. These drills often come with adjustable torque settings and reversible operation to facilitate smooth tapping processes. Air tapping drills are available in various sizes to accommodate different tap sizes, ranging from small M3 threads to larger M12 threads.
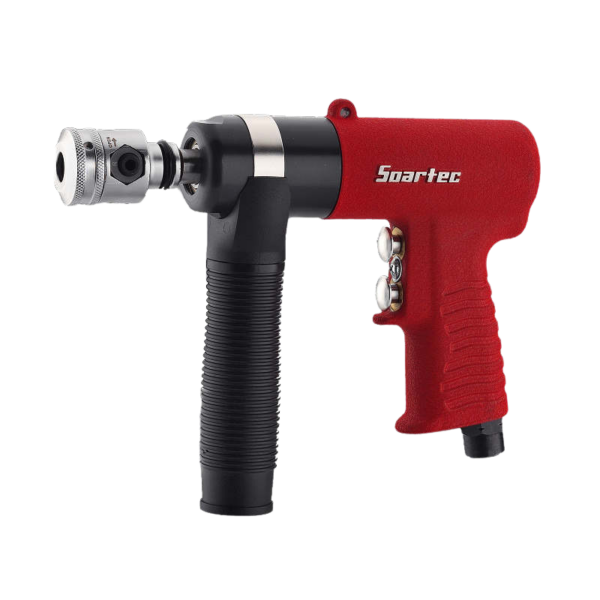
Advantages and Applications
Power and Efficiency
Pneumatic drill guns stand out for their impressive power-to-weight ratio. These tools deliver high torque and rapid drilling speeds, making them ideal for heavy-duty jobs. Unlike electric drills, pneumatic drill guns don’t require a heavy motor, resulting in a lightweight design that reduces operator fatigue. This combination of power and efficiency allows workers to tackle challenging tasks with ease, enhancing productivity in various industrial settings.
Precision and Control
The design of pneumatic drill guns, particularly pistol-grip air drills, offers exceptional control and precision. These tools provide consistent power output, allowing for accurate drilling in various materials. The ability to adjust air pressure through the compressor enables fine-tuning of the tool’s performance, ensuring optimal results for different applications. This level of control is crucial in industries where precision is paramount, such as automotive manufacturing and aerospace.
Durability and Longevity
Pneumatic drill guns are renowned for their durability and long-lasting performance. With fewer moving parts compared to electric tools, they require minimal maintenance and are less prone to breakdowns. The simple construction of these tools enhances their longevity, even under harsh conditions. This durability translates to cost-effectiveness, as pneumatic drill guns can withstand continuous use in demanding environments without frequent replacements.
Common Industrial Applications
The versatility of pneumatic drill guns makes them indispensable in various industries. In construction, they excel at creating foundations and breaking up pavement. Mining operations utilize these tools for extracting minerals from rock formations. The automotive sector relies on pneumatic drill gun for assembly tasks, while the manufacturing industry employs them for precision drilling in production lines. Their ability to function safely in wet or hazardous conditions further expands their applicability across diverse work environments. The air drill gun can also be used for non-automotive applications. Its power and precision make it ideal for tasks in construction, manufacturing, repairing and even DIY projects. From assembling furniture to installing fixtures, this tool’s versatility knows few bounds.
Maintenance and Safety
Proper Lubrication Techniques
To keep pneumatic drill guns in top condition, regular lubrication is crucial. Use the manufacturer-recommended oil, typically applying 10-15 drops into the air inlet before each use. For extended operations, reapply oil every few hours. Some tools, like pistol-grip air drills, benefit from daily lubrication. Avoid petroleum-based oils, as they can damage O-rings and other rubber components.
Air Supply Management
Proper air supply management is vital for the longevity of pneumatic drill gun. Install air filters to remove moisture and debris from the compressed air. Regularly check and clean air intake vents, and drain receiver tanks to prevent water accumulation. Maintain the correct air pressure as specified by the manufacturer, as excessive pressure can lead to tool damage and safety hazards. Soartec has compiled all the key points and important considerations regarding pressure conversion for you. Click to learn more.
Safety Protocols and PPE
When using pneumatic drill gun, safety should be a top priority. Always wear appropriate Personal Protective Equipment (PPE), including safety glasses, hearing protection, and gloves. For dusty environments, use a dust mask. Set up screens or shields to protect nearby workers from flying debris. Never point the drill gun at anyone, and always disconnect the air supply before performing maintenance or clearing jams.
Storage and Handling Best Practices
Store pneumatic drill gun in a clean, dry area to prevent moisture damage. Use silica packs to absorb excess humidity. When transporting the tool, avoid carrying it by the hose, as this can cause damage. Instead, hold it by the handle. Regularly inspect hoses for cuts, bulges, or wear, and replace them if defective. By following these maintenance and safety practices, you can ensure the longevity and safe operation of your pneumatic drill guns.
Conclusion
Pneumatic drill gun has become a game-changer in various industries, offering a perfect blend of power, precision, and durability. Their ability to handle tough materials and work in challenging environments has made them essential tools in construction, manufacturing, and maintenance. The wide range of available types, from straight air drills to specialized tapping models, ensures there’s a suitable option for almost every drilling task.
To get the most out of these powerful tools, proper maintenance and safety practices are crucial. Regular lubrication, careful air supply management, and adherence to safety protocols not only extend the life of the equipment but also protect operators from potential hazards. As technology advances, we can expect further improvements in pneumatic drill gun design, potentially leading to even more efficient and versatile tools in the future.