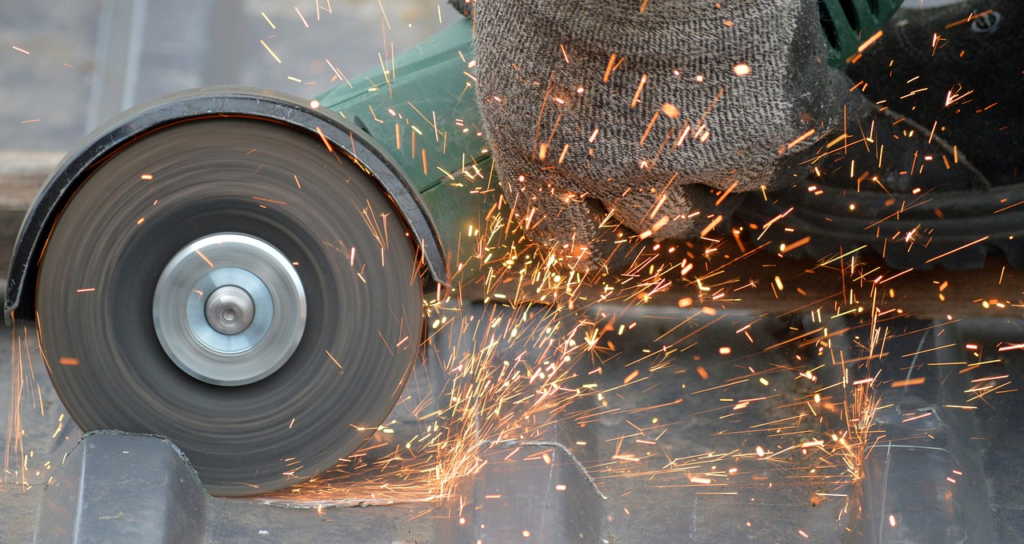
Professional-grade air grinder tool, such as the angle die grinder and pneumatic die grinder, deliver exceptional precision capabilities of 0.001 inches at operational speeds reaching over 20,000 RPM depends on different models. Metal fabrication shops, industrial facilities, and manufacturing units rely on these powerful pneumatic grinders for critical surface finishing and metalworking applications. Their specialized design combines raw power with exact control, making them essential equipment for precision-focused industrial operations.
The air grinder tool category features purpose-built variants engineered for specific industrial requirements – from aggressive material removal to detailed finishing work. Each model maintains consistent cutting force and superior handling characteristics across metals, composites, and specialized materials. This technical guide examines the core mechanics, classification, optimization methods, and real-world applications of air grinding tool, providing industrial users with essential selection criteria for their specific operational needs.
Understanding Soartectools’ Air Grinder Tool
Professional air grinder tool from Soartectools feature sophisticated pneumatic motors that harness compressed air power for mechanical operation. The motor design employs precision-engineered rotors that generate high-velocity airflow through specialized blade configurations, similar to aerospace propulsion principles.
Core technical components define each unit of air compressor:
- High-output pneumatic motor deliver 4,500RPM~30,000RPM; Micro Air Die Grinder can even offer high power up to maximum 60,000RPM
- Engineered ergonomic grip surface for operational control
- Integrated air flow regulation system
Different Categories of Air Grinder Tool
Manufacturing specifications define distinct air grinder classifications, each purpose-built for specialized industrial requirements. Pneumatic die grinders lead the precision category, featuring motor with technical capabilities spanning 4,500 to 30,000 RPM depends on different models. These precision units excel in detailed metalwork operations.
Main types of air grinder tool:
- Air Straight Grinders are designed for linear grinding tasks, providing exceptional control and accuracy. These tools excel in extended grinding, sanding, and polishing operations, particularly on flat or hard-to-reach surfaces. Engineered for durability and precision, they minimize vibration and ensure consistent output in demanding applications.
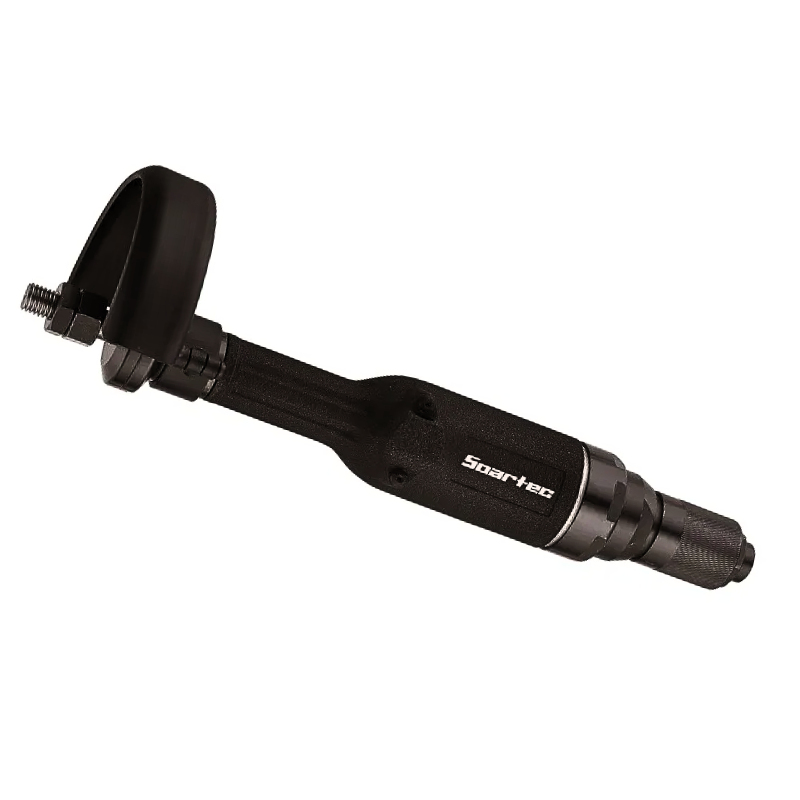
- Air Angle Grinders round out the primary equipment classifications. These production units accept wheel configurations from 2″ to 7″, offering rapid conversion between cutting, surface preparation, and coating removal functions through modular attachment systems.
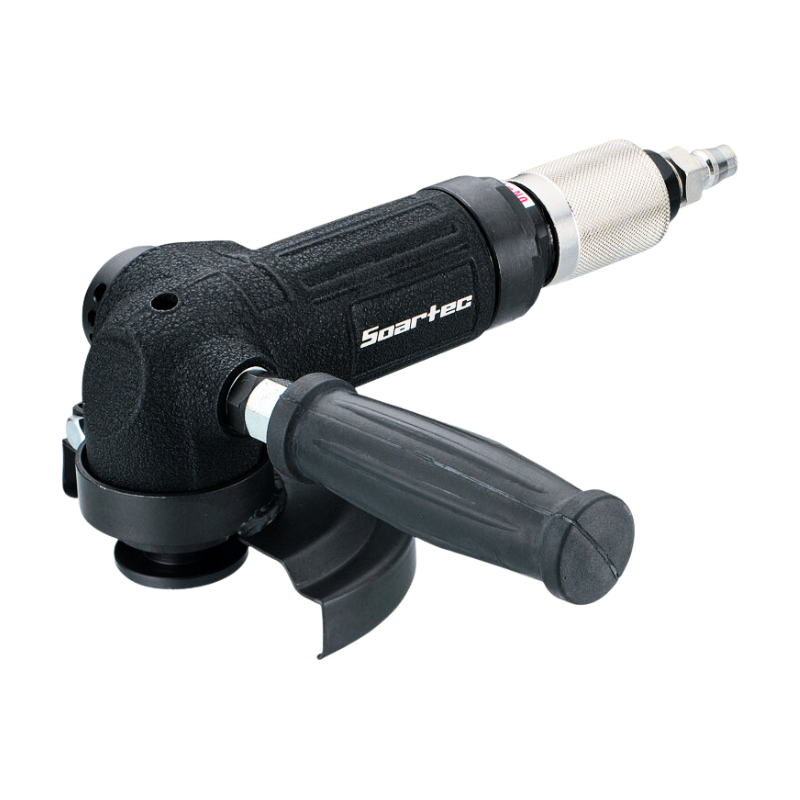
- Air Vertical Grinders showcase advanced power transfer through direct-drive engineering. Precision-engineered centrifugal governors maintain exact rotational specifications under substantial material loads.
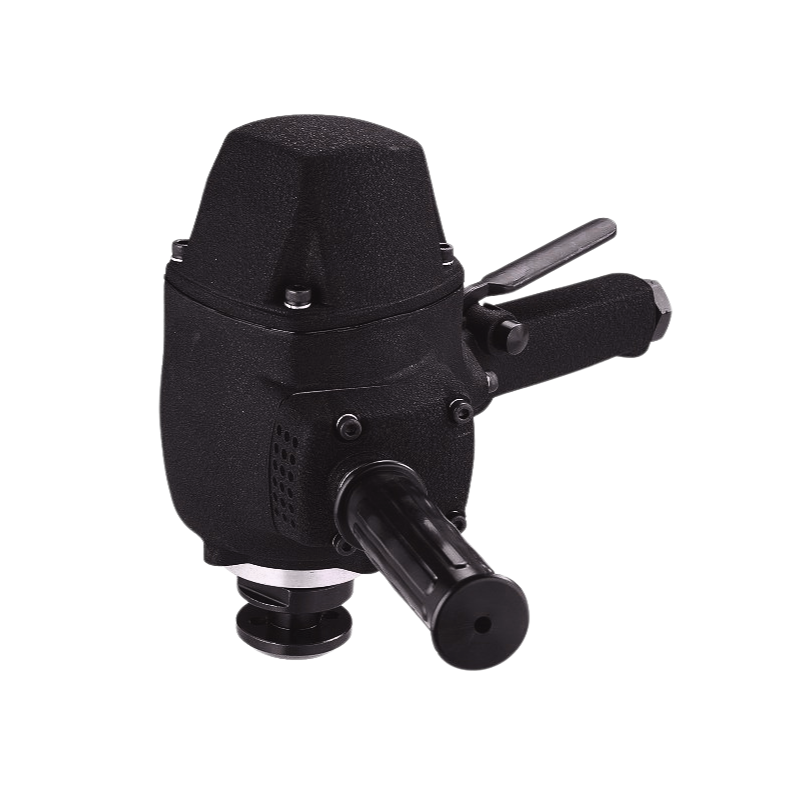
- Air Die Grinders specialize in high-precision work, perfect for intricate shaping, engraving, and finishing tasks. Lightweight and ergonomically balanced, these tools are built for maneuverability and control in tight spaces. Their compatibility with a wide range of attachments enhances their versatility for detailed craftsmanship.
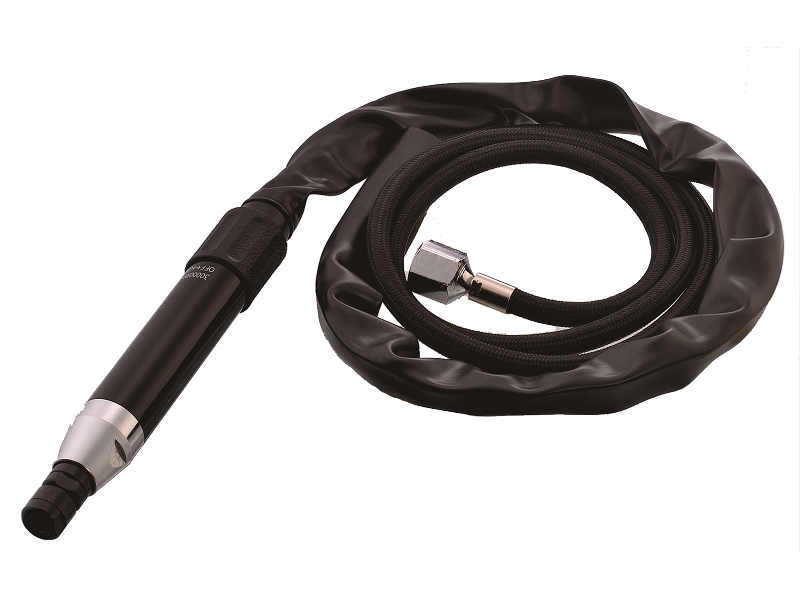
Micro Air Die Grinder 6mm (1/4″)
Equipment selection protocols prioritize application requirements, precision specifications, and spatial parameters. Manufacturing standards specify 90 PSI maximum operational pressure, ensuring repeatable performance across industrial applications.
Maximizing Performance
Technical excellence demands precise calibration of operational parameters combined with systematic maintenance protocols. Peak performance specifications require equipment selection based on optimized power-to-weight ratios aligned with specific production requirements.
Manufacturing standards specify 90 PSI operational pressure across industrial applications. Technical specifications warn against pressure variations – excessive levels risk component failure while insufficient pressure compromises output capabilities.
Production maintenance protocols specify:
- Systematic component cleaning and lubrication cycles
- Specified air filtration equipment installation
- Scheduled connection and supply line inspection
- Technical wheel maintenance procedures
Technical operation protocols specify 15-30° surface engagement angles for optimal stock removal. Precision control eliminates excessive force application, protecting equipment integrity while maintaining production standards. Equipment warm-up cycles require graduated load application, preventing thermal stress damage.
Applications and Uses
Production facilities across industrial sectors depend on air grinder tools for precision material processing requirements. These units demonstrate exceptional capabilities across diverse manufacturing environments.
Manufacturing operations utilize these precision grinders for metal fabrication processes, surface preparation protocols, and component production. Superior torque specifications and speed control features enable advanced production rates while maintaining exact tolerances for deburring and edge finishing operations.
Automotive production facilities showcase specialized applications:
- Vehicle body surface preparation protocols
- Coating removal and rust mitigation procedures
- Show-quality surface finishing operations
- Engine component precision machining
Industries that require the use of air grinder tools:
- Marine Sector Applications
- Woodworking Operations
- Construction Specifications
- Aviation Industry Applications
Conclusion
Production facilities worldwide recognize air grinder tools as mission-critical equipment for precision operations. Technical specifications highlight operational capabilities reaching 20,000 RPM, while engineered safety features – self-locking throttle mechanisms and rear exhaust systems – ensure workplace protection.
Equipment classifications span FOUR primary categories: straight grinders, angle grinders, vertical and die grinders. Each unit delivers specialized capabilities with power ratings from 4,500RPM to 60,000RPM.
Production standards specify systematic maintenance protocols – component cleaning, lubrication cycles, filtration systems – supporting peak performance at 90 PSI operational pressure.
Manufacturing sectors demonstrate diverse applications across automotive, marine, and construction operations. Production capabilities range from precision deburring procedures to large-scale surface preparation protocols. Superior speed control, structural durability, and precision engineering position these air tools as essential equipment for material processing operations demanding both power and accuracy.
Click to see all models of air grinder tool!
FAQs
Q1. What are the main applications of air grinder tools?
Air grinder tools, including the right angle die grinder and straight die grinder, are versatile and widely used in manufacturing, automotive, marine, and construction industries. They excel in tasks such as metal shaping, surface finishing, paint stripping, rust removal, polishing, ductwork fabrication, woodworking, and concrete surface preparation.
Q2. How do air grinder tools differ from electric grinders?
Air grinder tools operate using compressed air, which allows them to run cooler and maintain longevity due to fewer moving parts. They are generally lighter, safer for extended use, and can achieve higher RPM (up to 60,000 RPM) while producing less noise compared to their electric counterparts.
Q3. What are the key categories of air grinder tools?
The main categories of air grinder tools include straight grinders, angle grinders, vertical and die grinders.
Q4. How can I maximize the performance of my air grinder tool?
To optimize performance, maintain the tool at 90 PSI pressure, regularly clean and lubricate moving parts, use proper air filtration systems, and inspect air hoses and connections routinely. Also, allow the tool to do the work by maintaining a 15-30° angle to the work surface and avoid applying excessive pressure.
Q5. What safety features are typically included in modern air grinder tools?
Modern air grinder tools often come equipped with safety features such as self-locking throttles to prevent accidental starts and front exhaust or rear exhaust systems that direct air away from the work area. Their lightweight composite housing and cool operation also contribute to safer usage compared to electric-powered alternatives.