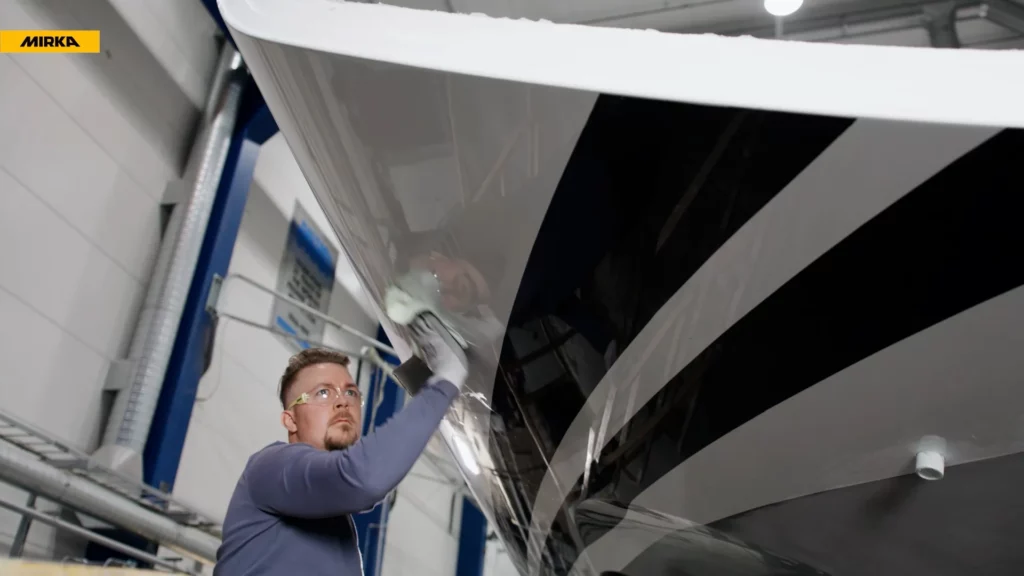
Understanding the Essence of Water Sanding
Fiberglass surfaces, with their sleek and glossy appearance, are a true testament to modern craftsmanship. However, maintaining their pristine condition can be a daunting task, especially when faced with the challenges of oxidation, scratches, and imperfections. Enter the realm of water sanding, a revolutionary technique that harnesses the power of water to deliver unparalleled results. This comprehensive guide will unveil the intricacies of using a water sander on fiberglass surfaces, equipping you with the knowledge and skills to achieve a flawless finish every time.
The Advantages of Water Sanding Fiberglass
Conventional dry sanding methods can be messy, hazardous, and often leave behind unsatisfactory results. In contrast, water sanding offers a multitude of benefits that make it the preferred choice for professionals and enthusiasts alike:
- Reduced Dust and Debris: By incorporating water into the sanding process, the amount of airborne particles and dust is significantly minimized, creating a safer and more pleasant working environment.
- Enhanced Surface Smoothness: The lubrication provided by water allows for a finer and more uniform sanding action, resulting in a smoother and more consistent finish.
- Improved Precision and Control: The water acts as a cooling agent, preventing the buildup of heat and friction, enabling greater control and precision during the sanding process.
- Versatility Across Materials: Water sanding is not limited to fiberglass alone; it can be effectively utilized on a wide range of materials, including wood, metal, and various composites.
Preparing for Water Sanding Success
Before embarking on your water sanding journey, it is crucial to gather the necessary tools and materials. Ensure you have the following items at your disposal:
- A high-quality water sander, preferably one with adjustable water flow and pressure settings for optimal control.
- A selection of abrasive pads or discs in varying grits, ranging from coarse to fine, to accommodate different stages of the sanding process.
- A reliable water source, such as a garden hose or a dedicated water tank, to ensure a continuous supply of water during the sanding process.
- Personal protective equipment (PPE), including safety glasses, gloves, and a respirator, to safeguard against any potential hazards.
- A sturdy work surface or platform to support the fiberglass component during sanding.
- Cleaning supplies, such as microfiber cloths and specialized cleaners, to prepare the surface and remove any residual debris.
The Art of Surface Preparation
Proper surface preparation is the foundation of a successful water sanding project. Follow these steps to ensure a smooth and efficient process:
- Thorough Cleaning: Begin by meticulously cleaning the fiberglass surface, removing any dirt, grease, or contaminants that may interfere with the sanding process. Use a degreaser or a specialized fiberglass cleaner to achieve optimal results.
- Identifying Imperfections: Carefully inspect the surface, taking note of any scratches, oxidation, or other defects that require attention. This will help you determine the appropriate grit levels and sanding techniques to employ.
- Masking and Protection: If necessary, mask off any areas that you do not wish to sand, such as hardware, trim, or adjacent surfaces. This will prevent accidental damage and ensure a clean and defined work area.
- Securing the Workpiece: Ensure that the fiberglass component is securely mounted or clamped to the work surface to prevent any movement or shifting during the sanding process.
Grit Selection and Progressive Sanding
The key to achieving a flawless finish lies in the strategic selection and progression of grit levels. Here’s a recommended approach:
- Coarse Grit Sanding (80-120 grit): For heavily oxidized or severely damaged surfaces, start with a coarse grit abrasive to remove the bulk of the imperfections. Apply moderate pressure and work in a systematic pattern, ensuring even coverage.
- Medium Grit Sanding (180-220 grit): Once the initial defects have been addressed, transition to a medium grit abrasive. This step will help refine the surface and prepare it for the finer grits.
- Fine Grit Sanding (320-400 grit): As you progress, switch to a fine grit abrasive to further smooth and level the surface, eliminating any remaining scratches or imperfections.
- Final Polishing (600-800 grit): For a truly mirror-like finish, consider employing ultra-fine grit abrasives or polishing pads. This final step will impart a deep, glossy shine to the fiberglass surface.
Remember, the key to success is patience and attention to detail. Take your time and ensure that each grit level has thoroughly prepared the surface for the next step.
Mastering Water Flow and Pressure
One of the unique advantages of water sanding is the ability to precisely control the water flow and pressure. Adjusting these settings can significantly impact the effectiveness and efficiency of the sanding process:
- Water Flow: Maintaining an optimal water flow is essential for ensuring a smooth and consistent sanding action. Too little water can lead to dry spots and potential surface damage, while excessive water can create excessive splashing and reduce visibility.
- Water Pressure: The water pressure plays a crucial role in the aggressiveness of the sanding action. Higher pressure settings can be employed for more aggressive material removal, while lower pressure settings are ideal for finer finishing work.
Experiment with different water flow and pressure combinations to find the perfect balance for your specific project and desired outcome.
Techniques for Efficient Water Sanding
While water sanding may seem straightforward, mastering the proper techniques can elevate your results to new heights. Consider the following approaches:
- Overlapping Passes: Ensure consistent and even coverage by overlapping each sanding pass by approximately 50%. This technique will prevent the formation of unsightly ridges or uneven areas.
- Varying Sanding Patterns: Alternate between horizontal, vertical, and diagonal sanding patterns to avoid creating directional scratches or patterns in the fiberglass surface.
- Maintaining Consistent Pressure: Apply even and consistent pressure throughout the sanding process to achieve a uniform finish. Avoid applying excessive force, as this can lead to gouging or uneven material removal.
- Frequent Abrasive Replacement: Replace abrasive pads or discs regularly to maintain their effectiveness and prevent the transfer of contaminants or debris back onto the surface.
Addressing Challenging Areas
Fiberglass components often feature intricate curves, edges, and contours that can pose unique challenges during the sanding process. Here are some strategies to tackle these areas effectively:
- Contoured Surfaces: For curved or contoured areas, consider using specialized contour sanding tools or flexible abrasive pads that can conform to the shape of the surface.
- Edges and Corners: Pay close attention to edges and corners, as these areas are prone to excessive material removal or rounding. Use a combination of hand sanding and precise water sanding techniques to achieve a crisp and well-defined finish.
- Recessed Areas: Recessed or hard-to-reach areas may require the use of specialized sanding attachments or tools to ensure thorough coverage and a consistent finish.
Post-Sanding Cleanup and Protection
Once you have achieved the desired level of smoothness and finish, it’s essential to properly clean and protect the newly sanded surface. Follow these steps:
- Thorough Rinsing: Use a clean water source to thoroughly rinse the sanded surface, removing any residual debris or contaminants.
- Drying: Allow the surface to dry completely, either through air drying or by gently wiping it down with a clean, lint-free cloth.
- Surface Inspection: Carefully inspect the sanded surface for any remaining imperfections or areas that require additional attention.
- Surface Protection: Apply a high-quality marine-grade wax, sealant, or clear coat to protect the freshly sanded surface from future oxidation, UV damage, and environmental exposure.
Maintenance and Longevity
Proper maintenance is key to ensuring the longevity of your water-sanded fiberglass surfaces. Implement the following practices to preserve their pristine condition:
- Regular Cleaning: Establish a routine for cleaning and inspecting the fiberglass surfaces, using mild soap and water or specialized cleaners designed for marine applications.
- Wax Application: Periodically apply a fresh coat of marine-grade wax or sealant to maintain the protective barrier and enhance the shine.
- Avoid Abrasive Cleaners: Steer clear of harsh or abrasive cleaners, as they can potentially damage the fiberglass surface and diminish the effects of your water sanding efforts.
- UV Protection: When possible, store or cover the fiberglass components to minimize exposure to direct sunlight and UV radiation, which can accelerate oxidation and fading.
Embracing Innovation: The Soartec Air Water Sander
In the ever-evolving world of surface finishing, Soartec has introduced a groundbreaking solution: the Air Water Sander. This innovative tool combines the power of water sanding with advanced air technology, offering a truly seamless and precise sanding experience:
- Reduced Dust and Mess: The Air Water Sander utilizes a unique water-based sanding system, virtually eliminating the generation of airborne dust and debris, ensuring a cleaner and safer work environment.
- Enhanced Precision and Control: The integrated air delivery system provides precise control over water flow and pressure, allowing for unparalleled accuracy and finesse during the sanding process.
- Versatile Application: Designed for versatility, the Air Water Sander can be used on a wide range of materials, including fiberglass, wood, metal, and various composites, making it an indispensable tool for professionals and enthusiasts alike.
- Optimized Surface Finish: By combining the benefits of water sanding with advanced air technology, the Air Water Sander delivers a superior surface finish, leaving behind a smooth, mirror-like appearance that is sure to impress.
Embrace the future of surface finishing with the Soartec Air Water Sander, and experience the ultimate in precision, efficiency, and professional-grade results.
Conclusion
Mastering the art of water sanding on fiberglass surfaces is a journey that requires patience, attention to detail, and a commitment to excellence. By following the comprehensive guidelines outlined in this guide, you will be equipped with the knowledge and skills necessary to achieve flawless finishes that not only enhance the aesthetic appeal of your fiberglass components but also extend their longevity and durability.
Remember, the key to success lies in proper preparation, meticulous technique, and a dedication to continuous improvement. Embrace the power of water sanding, and unlock a world of pristine fiberglass finishes that will leave a lasting impression on all who witness your craftsmanship.
To read more about water sander: Top 10 Benefits of Using a Water Sander on Metal Surfaces